- Overview
Ryson’s Bucket Elevators combine vertical and horizontal transportation of bulk materials in one integral unit and represent a unique and highly effective solution to your bulk material conveyor needs.
Ryson Bucket Elevators have earned a reputation for being the most durable bulk material conveyors in the marketplace. Their robust and forward-thinking design combines a number of features—from gentle handling and rugged construction to minimal maintenance and modular design—businesses have come to benefit from and deeply value.
Ryson Bucket Conveyors’ signature feature is that they are completely enclosed and overlapping pivoting buckets, that prevent spillage and keep out foreign debris.
Additionally, our Bucket Elevators stand out compared with our competitors because they are completely modular, have pivoting buckets and can have multiple inlets and outlets.
Ryson’s Bucket Conveyors are designed for heavy-duty operations and long lifespans. They can be delivered in powder-coated carbon-steel, stainless-steel or wet environment versions.
Our Bucket Elevators with multiple outlets feature selective bucket-tipping capabilities. This is accomplished by an air-actuated tipping ramp. The last tipping ramp is always in a fixed position, ensuring that all buckets are emptied.
- Gallery
- Features & Benefits
Our Bucket Elevators are designed for gentle handling and well-suited to transport a broad range of bulk products in the food, agriculture, pharmaceutical, cosmetic, chemical, ceramic, glass, recycling, building, metallurgical and other industries.
Our Bucket Conveyor can be configured with multiple inlets or outlets that feature selective bucket-tipping capabilities. This is accomplished by an air-actuated tipping ramp. The last tipping ramp is always in a fixed position, ensuring that all buckets are emptied.
Ryson Bucket Elevators are at robust completely enclosed design yet offer gentle handling of all kinds of products.
These buckets overlap at the inlets to prevent spillage and can be selectively tipped at the outlets.
The chain is a 2-inch plated roller chain with a hollow pin shaft and 1⅛-inch diameter rollers. The rolling surface is made of polyurethane, providing smooth and quiet operation. The buckets are made of food-grade-reinforced polyamide, complying with U.S. Food and Drug Administration (FDA) standards. The buckets are molded in one piece and can handle temperatures from –5 to +200 degrees Fahrenheit.
Additionally, flanges are provided at the inlets and outlets to facilitate easy attachment of extended funnels, shoots or tubes.
Ryson Bucket Elevators are built using high-quality components. As such, you can expect to face only minimal maintenance when working with our models. All our Bucket Elevator models have easily removable inspection covers and a conveniently located inspection window.
Our Bucket Elevators feature drawers located underneath the horizontal sections to facilitate fast and easy cleaning. The inside walls are smooth, helping prevent dust buildup. All bearings are mounted outside for easy access.
Our Bucket Elevators are also equipped with a quick-release mechanism to facilitate fast installation or removal of buckets as well as an automatic chain tensioning device and built-in overload protection.
A variable frequency drive, also known as a VFD, is required for proper operation.
Our Bucket Elevators are completely enclosed, helping to mitigate foreign debris.Their construction also offers inspection windows and access ports to simplify cleaning and maintenance procedures.
- Specs & Configurations
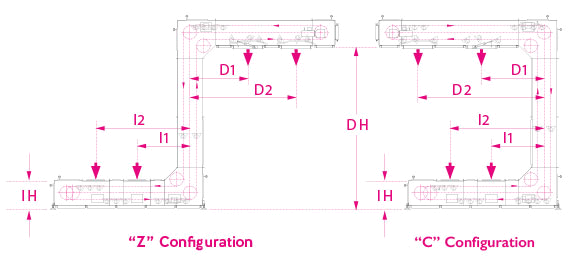
Most Common Models
Width
CuFT/HR
Width
Configurations
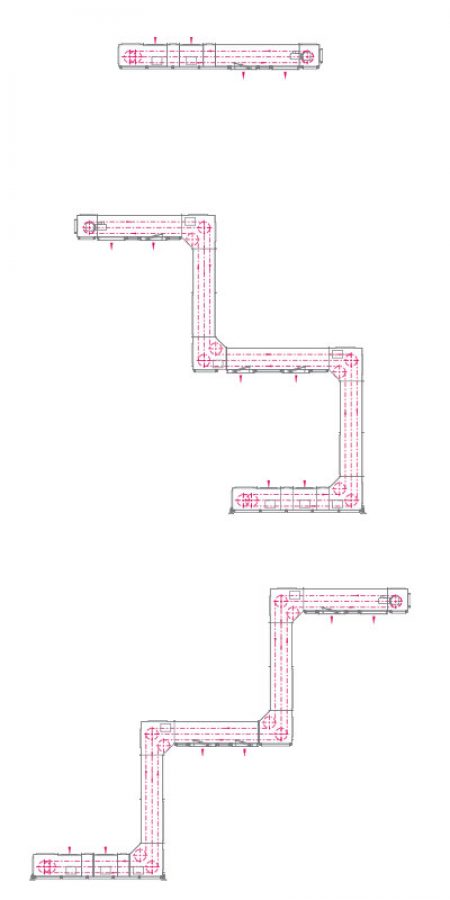
Ryson Bucket Elevators’ modular design enables us to customize with ease and makes your bucket elevator versatile as well as easy to install and modify. The most common configurations are our C and Z configurations, which are available with three different bucket sizes, yielding capacities up to 300, 700 or 1,800 cubic feet per hour. The buckets must be loaded with a controlled volume and across the full width of the buckets.
No matter the use case, the Ryson team is up to the challenge of finding solutions your business needs. Explore a special application for a custom-built bucket elevator we created for a customer needing to elevate lightweight cellulose material. You can also Download a printable RFQ Form.
- Videos
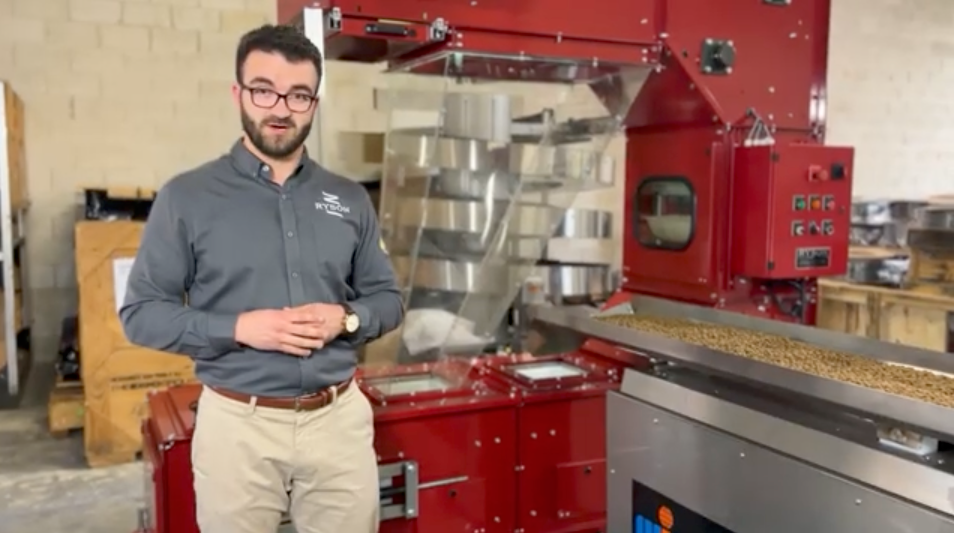
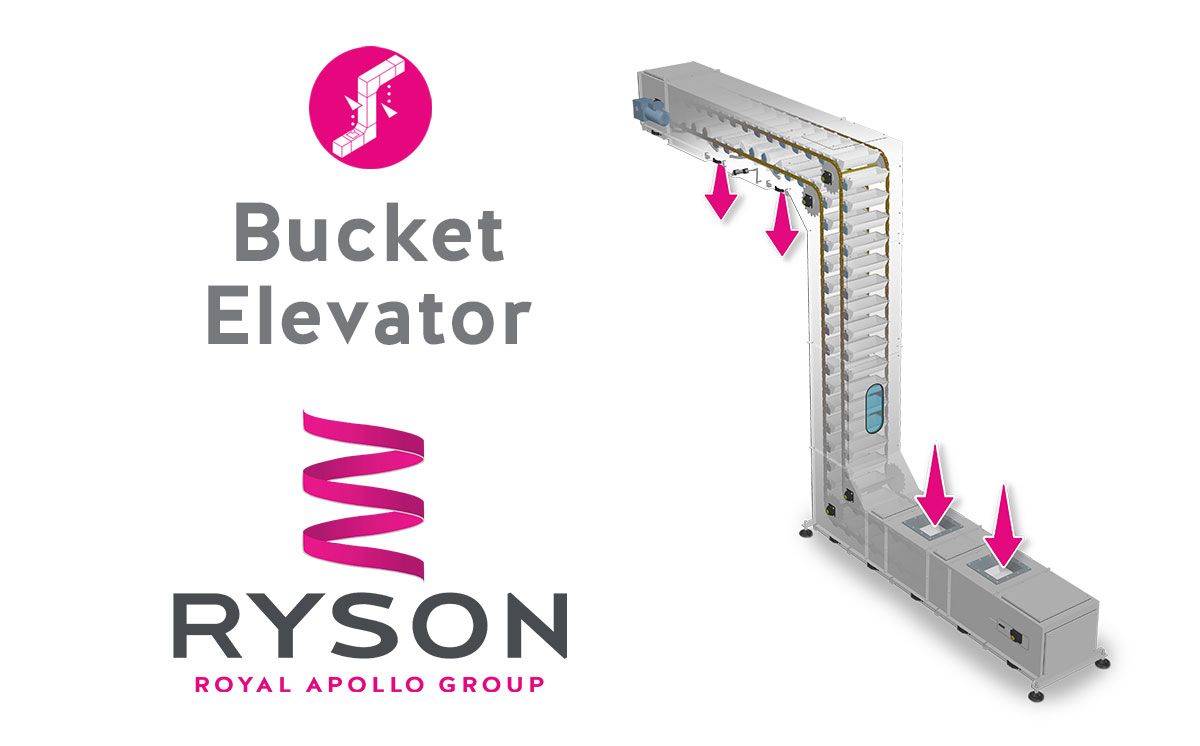
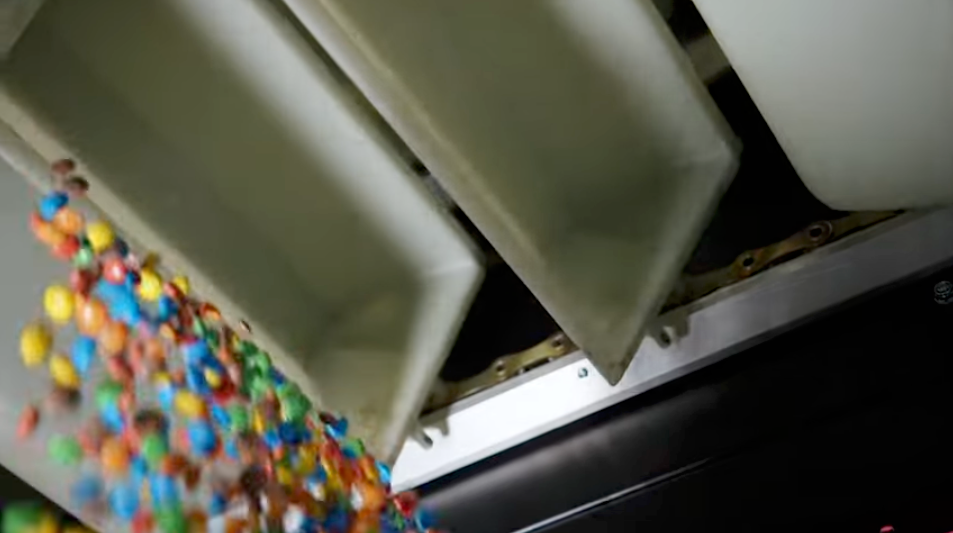
Related Articles
What Is a Bucket Elevator?
A bucket elevator, also known as a grain leg, is a highly efficient bulk material handling equipment designed to transport a wide variety of materials vertically. These materials can range from light to heavy and from fine particulates to larger bulk solids. Bucket elevators offer a reliable and cost-effective solution for industries such as food processing, agriculture, pharmaceuticals, mining, and more.
Ryson Bucket Elevators are state-of-the-art vertical conveying systems that combine vertical and horizontal transportation in a single, space-saving unit. Available in C- and Z-shaped configurations with three bucket size options, these elevators can move up to 300, 700, or 1,800 cubic feet of material per hour, providing flexibility and high capacity for businesses across various sectors.
How Does a Bucket Elevator Work?
Bucket elevators vertically transport bulk materials using a continuous loop of buckets attached to a belt or chain. The process begins with the buckets being loaded with material at the inlet point, either manually or through an automated feeding system. As the belt or chain moves, the buckets are carried upward, containing the material securely.
Upon reaching the discharge point at the top of the elevator, the buckets are tipped or inverted, emptying their contents into a discharge chute or onto another conveyor for further processing or storage. The empty buckets then continue to rotate, returning to the loading point at the bottom of the loop to start the cycle again.
Difference Between Belt Conveyor and Bucket Elevator
While both belt conveyors and bucket elevators are used for material handling, they have some key differences in terms of design, operation, and application. Belt conveyors are typically used for horizontal or slightly inclined transport of bulk materials over relatively long distances.
They consist of a continuous belt supported by rollers or a sliding bed, and the material is carried on top of the belt. In contrast, bucket elevators are used for vertical or steep-incline transport of materials over shorter distances. They consist of a series of buckets attached to a belt or chain, which scoops up the material at the bottom and discharges it at the top.
Bucket elevators are generally more compact and can handle a wider range of materials compared to belt conveyors, but they have limitations in terms of maximum height and capacity. The choice between a belt conveyor and a bucket elevator depends on factors such as the material properties, required capacity, elevation change, and available space.
Ryson Bucket Elevators
Ryson’s continuous discharge Bucket Elevators are revolutionizing bulk material handling by offering a unique and highly effective solution that outperforms traditional conveying systems. With their innovative design and superior build quality, Ryson Bucket Elevators have become the preferred choice for industries demanding reliability, efficiency, and versatility.
One of the standout features of Ryson Bucket Elevators is their fully enclosed design, which incorporates overlapping pivoting buckets. This not only prevents material spillage and contamination but also ensures a clean and safe working environment. The enclosed system keeps foreign debris out, maintaining the integrity of the transported materials.
Moreover, Ryson Bucket Elevators are entirely modular, allowing for easy customization and adaptation to suit specific application requirements. The modular design enables the integration of multiple inlets and outlets, providing unmatched flexibility in material handling processes.
Download Bucket Elevator Spec Sheet
See Ryson Bucket Elevators in Action
To witness the impressive performance and capabilities of Ryson Bucket Elevators firsthand, watch our informative video showcasing these cutting-edge vertical conveying systems in operation.
Key Features of Ryson Bucket Elevators
Gentle Material Handling
Ryson Bucket Elevators are engineered to provide gentle handling of a wide range of bulk materials, making them suitable for delicate products in industries such as food processing, pharmaceuticals, cosmetics, and more. The overlapping bucket design prevents material spillage, while the controlled tipping action at the outlets ensures precise and damage-free discharge.
Heavy-Duty Construction
Built to withstand the demands of intensive use, Ryson Bucket Elevators feature a robust and durable construction. Available in powder-coated carbon steel, stainless steel, or washdown versions, these elevators are designed for long-lasting performance in various environments. The 2-inch plated roller chain with hollow pin shafts and 1⅛-inch diameter rollers provides smooth and quiet operation, while the polyurethane rolling surface ensures long-term reliability.
Low Maintenance Requirements
Ryson Bucket Elevators are crafted using premium components, resulting in minimal maintenance needs. The elevators feature easily accessible inspection covers, conveniently located inspection windows, and drawers underneath the horizontal sections for quick and easy cleaning. The smooth interior walls prevent dust accumulation, and the externally mounted bearings simplify maintenance tasks.
Customizable Modular Design
The modular design of Ryson Bucket Elevators allows for seamless customization to meet specific application requirements. The C and Z configurations, combined with the three available bucket sizes, provide a wide range of capacities up to 1,800 cubic feet per hour. This versatility enables businesses to tailor their conveying solution to their unique needs, optimizing efficiency and productivity.
Optional Features for Enhanced Performance
To further enhance the performance and functionality of Ryson Bucket Elevators, several optional features are available:
Advanced control systems for precise operation and monitoring
Dust-sealed enclosures for improved air quality and safety
Additional inspection windows for better visibility and maintenance access
Anti-static, metal-detectable, or stainless-steel buckets for specialized applications
Integrated cleaning stations for efficient and thorough maintenance
Stainless-steel or washdown versions for hygienic and corrosion-resistant operation
Find out More About Ryson and Its Green Products and Sustainability
Ryson is committed to providing green and sustainable conveying solutions that minimize environmental impact while maximizing efficiency. To learn more about Ryson’s eco-friendly products and sustainable practices, visit our website or contact our knowledgeable team today.
Applications and Industries
Ryson Bucket Elevators find extensive use in a wide range of industries, offering efficient and reliable vertical conveying solutions for diverse bulk materials. Some key industries and applications include:
Food Processing: Bucket elevators are essential for handling various food products, such as grains, flour, sugar, salt, and coffee beans, ensuring gentle and contamination-free transportation.
Agriculture: In the agricultural sector, bucket elevators are used for conveying seeds, fertilizers, and animal feed, streamlining storage and distribution processes.
Mining and Minerals: Bucket elevators are employed in the mining industry for conveying ores, coal, and other minerals, facilitating efficient material handling in challenging environments.
Chemical and Pharmaceutical: These industries rely on bucket elevators for the safe and precise handling of powders, granules, and pellets, maintaining product integrity and purity.
Recycling and Waste Management: Bucket elevators play a crucial role in recycling facilities, handling materials such as plastic, glass, and metal, enabling efficient sorting and processing.
Comparison with Other Conveying Methods
When considering vertical conveying solutions, bucket elevators offer several advantages over alternative methods:
Pneumatic Conveyors
While pneumatic conveyors can handle a wide range of materials, they have limitations in terms of distance and height. Bucket elevators, on the other hand, can efficiently transport materials over longer distances and greater heights, making them suitable for multi-story facilities.
Screw Conveyors
Screw conveyors are effective for short-distance vertical conveying but may cause damage to fragile materials due to the grinding action of the screw. Bucket elevators provide gentler handling, preserving product quality.
Belt Conveyors
Vertical belt conveyors can handle large capacities but may struggle with fine or powdery materials. Bucket elevators are designed to contain and transport a wide range of material sizes and types, ensuring minimal spillage and contamination.
Safety and Compliance
Ryson Bucket Elevators prioritize operator safety and compliance with industry regulations. Key safety features include:
- Enclosed Design. The fully enclosed construction of Ryson Bucket Elevators prevents material spillage and dust generation, creating a safer working environment.
- Dust Control. Optional dust-sealed enclosures and dust collection systems can be integrated to further minimize airborne particles and improve air quality.
- Emergency Stop Systems. Ryson Bucket Elevators can be equipped with emergency stop buttons and sensors to quickly halt operation in case of any safety concerns.
- Compliance. Ryson Bucket Elevators are designed to meet stringent industry standards and regulations, such as OSHA for workplace safety, FDA for food-grade materials, and ATEX for operation in potentially explosive atmospheres.
Capacity and Performance Metrics
Ryson Bucket Elevators offer a range of capacities to suit various application requirements. The capacity of a bucket elevator is influenced by factors such as:
- Bucket Size. Ryson offers three standard bucket sizes, providing capacities up to 300, 700, or 1,800 cubic feet per hour.
- Material Density. The density of the conveyed material directly impacts the volumetric capacity of the elevator. Ryson Bucket Elevators can be customized to accommodate materials with different densities.
- Elevator Speed. The speed of the bucket elevator can be adjusted to optimize throughput while maintaining gentle handling and minimizing material degradation.
Integration and System Design
Ryson Bucket Elevators can be seamlessly integrated into comprehensive material handling systems. Key considerations for system integration include:
Feeding and Discharge
Ryson Bucket Elevators can be equipped with various feeding options, such as hoppers, chutes, or rotary valves, ensuring a controlled and consistent material flow. Discharge can be achieved through gravity, pneumatic, or mechanical means, depending on the application requirements.
Control Systems
Advanced control systems, including PLC and HMI interfaces, can be integrated to monitor and control the operation of the bucket elevator, ensuring optimal performance and safety.
Automation
Ryson Bucket Elevators can be incorporated into automated material handling systems, enabling seamless integration with other equipment, such as conveyors, packaging machines, and palletizers.
Maintenance and Troubleshooting
Regular maintenance is crucial for ensuring the long-term reliability and performance of Ryson Bucket Elevators. A comprehensive maintenance plan should include:
- Routine Inspections. Regularly inspect the elevator for signs of wear, damage, or misalignment. Check the condition of buckets, chains, bearings, and other critical components.
- Lubrication. Properly lubricate chains and bearings according to the manufacturer’s guidelines to minimize friction and extend component life.
- Cleaning. Utilize the easily accessible inspection covers and cleaning drawers to remove any accumulated debris or residue from the elevator, maintaining optimal performance and hygiene.
- Troubleshooting. Common issues, such as unusual noises, vibrations, or reduced capacity, can often be resolved by identifying and addressing the root cause. Consult the manufacturer’s troubleshooting guide or contact Ryson’s technical support team for assistance.
Future Developments and Innovations
Ryson is committed to staying at the forefront of bucket elevator technology, continuously researching and developing innovations to enhance performance, efficiency, and sustainability. Some areas of focus include:
- Smart Sensors and Predictive Maintenance. Integrating advanced sensor technology and data analytics to monitor elevator performance in real-time, enabling predictive maintenance and reducing unplanned downtime.
- Energy Efficiency. Developing energy-efficient drive systems and optimized bucket designs to reduce power consumption and operating costs.
- Lightweight Materials. Exploring the use of advanced composite materials for bucket construction, reducing weight and improving elevator efficiency.
By continually pushing the boundaries of bucket elevator technology, Ryson aims to provide customers with cutting-edge solutions that drive productivity, reliability, and sustainability in bulk material handling applications.
Download Bucket Elevator Spec Sheet
For more details on Ryson’s Vertical Conveyors, please visit our YouTube channel and read current news and installation stories about our Bucket Elevators on the Ryson Blog.
See Bucket Elevator Blog Posts
Find out More About Ryson and Its Green Products and Sustainability
Types of Bucket Elevators
Centrifugal Bucket Elevator
Centrifugal bucket elevators, also known as high-speed elevators, are designed for handling free-flowing materials at high capacities. The buckets are mounted on a high-speed belt or chain, and the material is discharged by centrifugal force at the head pulley. This type of elevator is suitable for handling materials such as grains, pellets, and granules, where gentle handling is not a primary concern. Centrifugal bucket elevators offer high throughput rates and are commonly used in industries such as agriculture, food processing, and bulk material handling.
Continuous Bucket Elevator
Continuous bucket elevators, also referred to as slow-speed elevators, are characterized by closely spaced buckets on a belt or chain that operate at lower speeds compared to centrifugal elevators. The material is discharged by gravity as the buckets pass over the head pulley. Continuous bucket elevators are ideal for handling fragile or abrasive materials that require gentle handling, such as food products, chemicals, and minerals. They offer precise control over the material flow and are suitable for applications requiring minimal breakage or degradation of the material being conveyed.
Vertical Bucket Elevator
Vertical bucket elevators are designed for conveying materials in a straight vertical path, making them suitable for applications with limited horizontal space. The buckets are attached to a belt or chain, and the material is scooped up from the boot section and discharged at the head pulley. Vertical bucket elevators are commonly used in industries such as cement, mining, and power generation, where high lifting heights and capacities are required. They offer a compact footprint and can be easily integrated into existing plant layouts.
Inclined Bucket Elevator
Inclined bucket elevators are used for conveying materials at an angle, typically between 45° and 70° from the horizontal. The buckets are mounted on a belt or chain, and the material is picked up from the boot section and discharged at the head pulley. Inclined bucket elevators are suitable for handling materials that tend to slide or roll back, such as wet or sticky substances. They are commonly used in industries such as food processing, chemical manufacturing, and waste management, where gentle handling and controlled discharge are essential.
Z-Type Bucket Elevator
Z-type bucket elevators, also known as zig-zag elevators, are designed with a series of intermediate pulleys that allow the conveyor to change direction and form a “Z” shape. This configuration enables the elevator to convey materials horizontally, vertically, and then horizontally again, making it suitable for applications with limited space or where multiple discharge points are required. Z-type bucket elevators are commonly used in industries such as packaging, pharmaceuticals, and food processing, where flexibility and compact design are crucial.
Chain Bucket Elevator
Chain bucket elevators use a chain as the conveying medium, with buckets attached at regular intervals. The chain is driven by sprockets at the head and tail sections, and the buckets scoop up the material from the boot and discharge it at the head. Chain bucket elevators are known for their durability and reliability, making them suitable for handling abrasive or heavy materials such as aggregates, minerals, and coal. They are commonly used in industries such as mining, cement, and power generation, where robust construction and high capacities are required.
Belt Bucket Elevator
Belt bucket elevators use a reinforced belt as the conveying medium, with buckets attached to the belt at regular intervals. The belt is driven by pulleys at the head and tail sections, and the buckets pick up the material from the boot and discharge it at the head. Belt bucket elevators offer smooth operation and are suitable for handling fragile or delicate materials that require gentle handling. They are commonly used in industries such as food processing, pharmaceuticals, and chemical manufacturing, where product integrity is of utmost importance.
Bucket Elevator Components and Specifications
Buckets
Buckets are the primary components responsible for carrying the material being conveyed. They come in various types, materials, and dimensions to suit different applications. Common bucket types include:
- Deep-drawn buckets: Formed from a single piece of metal, offering high strength and durability.
- Fabricated buckets: Constructed from multiple pieces of metal, allowing for customization and complex shapes.
- Plastic buckets: Lightweight and corrosion-resistant, suitable for handling food products and chemicals.
- Nylon or polyurethane buckets: Abrasion-resistant and suitable for handling highly abrasive materials.
Bucket materials include steel, stainless steel, aluminum, plastic, and various alloys, selected based on the material being handled and the operating environment. Bucket dimensions, such as width, height, and capacity, are determined by the required throughput and the properties of the material being conveyed.
Belts and Chains
Belts and chains are the conveying media that carry the buckets and transmit the drive force. Belts are typically reinforced with fabric or steel cords to provide high tensile strength and durability. Belt materials include rubber, PVC, and polyurethane, selected based on the operating conditions and the material being handled. Chains, on the other hand, are constructed from steel or various alloys and are suitable for high-load applications. Chain types include:
- Roller chains: Commonly used in chain bucket elevators, offering high strength and durability.
- Leaf chains: Provide a larger bearing surface and are suitable for high-speed applications.
- Drag chains: Used in specialized elevators for handling difficult materials.
Belt and chain specifications, such as width, thickness, and breaking strength, are determined based on the required tensile strength and the operating conditions. Fasteners, such as bolts and rivets, are used to attach the buckets to the belt or chain, while splicing methods, such as vulcanized or mechanical splicing, are employed to join belt ends.
Pulleys and Sprockets
Pulleys and sprockets are the components that drive and guide the belt or chain, respectively. Head pulleys are located at the top of the elevator and are responsible for driving the belt or chain. Tail pulleys are located at the bottom of the elevator and serve to maintain belt or chain tension and guide the returning side. Take-up pulleys are used to adjust the tension and compensate for belt or chain elongation. Sprockets are used in chain bucket elevators to engage the chain and transmit the drive force.
Pulley and sprocket materials include cast iron, steel, and various alloys, selected based on the required strength and durability. Lagging materials, such as rubber or ceramic, are often applied to the pulley surface to improve traction and extend the belt life.
Casings and Supports
Casings are the enclosures that contain the bucket elevator components and guide the material flow. They are typically constructed from steel or stainless steel and are designed to withstand the material loads and operating conditions. Casing designs include:
- Sectional casings: Consisting of modular sections bolted together, allowing for easy installation and maintenance.
- Welded casings: Offering high strength and rigidity, suitable for heavy-duty applications.
- Dust-tight casings: Designed to contain dust and prevent contamination of the surrounding environment.
Supports, such as trusses or towers, are used to provide structural stability and maintain the alignment of the bucket elevator components. They are designed to withstand the static and dynamic loads imposed by the elevator and are typically constructed from steel or various alloys.
Drive Systems
Drive systems are responsible for providing the power and torque required to operate the bucket elevator. They consist of motors, gearboxes, and backstops. Motors are selected based on the required power and speed, with common types including electric, hydraulic, and pneumatic motors. Gearboxes are used to reduce the motor speed and increase the torque, with helical, bevel, and planetary gearboxes being common types. Backstops are used to prevent reverse rotation of the elevator and protect the drive components from damage.
Drive system specifications, such as power rating, speed, and torque, are determined based on the required throughput, lift height, and material properties. Proper sizing and selection of drive components are crucial for ensuring efficient and reliable operation of the bucket elevator.
Feeding and Discharge Arrangements
Feeding arrangements are used to introduce the material into the bucket elevator at a controlled rate. Common feeding arrangements include:
- Hoppers: Used to store and gravity-feed the material into the elevator boot.
- Chutes: Used to direct the material flow from upstream conveying equipment into the elevator.
- Rotary valves: Used to meter the material flow and prevent air leakage in pneumatic conveying systems.
Discharge arrangements are used to direct the material flow from the elevator head to downstream equipment. Common discharge arrangements include:
- Spouts: Used to guide the material flow to a specific location or equipment.
- Chutes: Used to direct the material flow and control the discharge trajectory.
- Valves: Used to control the material flow rate and direct the flow to multiple destinations.
Proper design and selection of feeding and discharge arrangements are essential for ensuring efficient material flow and minimizing spillage and dust generation.
Bucket Elevator Design and Calculations
Capacity Calculations and Formulas
Bucket elevator capacity refers to the amount of material that can be conveyed per unit time, typically expressed in tons per hour (TPH) or cubic meters per hour (m³/h). Capacity calculations are essential for sizing the elevator components and selecting the appropriate drive system. The basic formula for calculating the capacity is:
Capacity = Bucket Volume × Bucket Spacing × Belt/Chain Speed × Bucket Fill Factor
Where:
- Bucket Volume: The volumetric capacity of a single bucket, typically provided by the manufacturer.
- Bucket Spacing: The distance between consecutive buckets, determined based on the material properties and required throughput.
- Belt/Chain Speed: The linear speed of the belt or chain, selected based on the required capacity and material properties.
- Bucket Fill Factor: The percentage of the bucket volume that is actually filled with material, typically ranging from 70% to 95%.
Additional factors, such as material density, angle of repose, and elevation change, are also considered in the capacity calculations to ensure accurate sizing and selection of the elevator components.
Speed and Power Requirements
The speed and power requirements of a bucket elevator are determined based on the required capacity, lift height, and material properties. The belt or chain speed is selected to ensure efficient material pickup and discharge while minimizing wear and impact on the components. Common belt speeds range from 0.5 to 2 m/s, while chain speeds are typically lower, ranging from 0.2 to 0.6 m/s.
The power required to operate the bucket elevator is calculated based on the lifting force, frictional losses, and drive efficiency. The lifting force is determined by the weight of the material being conveyed and the lift height, while frictional losses are influenced by factors such as the belt or chain tension, pulley or sprocket efficiency, and bearing losses. Drive efficiency depends on the motor and gearbox selection and typically ranges from 85% to 95%.
The power requirement formula is:
Power = (Lifting Force + Frictional Losses) / Drive Efficiency
Where:
- Lifting Force: The product of the material weight and the lift height.
- Frictional Losses: The sum of the belt or chain tension, pulley or sprocket losses, and bearing losses.
- Drive Efficiency: The combined efficiency of the motor and gearbox.
Proper selection of the speed and power requirements ensures efficient and reliable operation of the bucket elevator while minimizing energy consumption and component wear.
Bucket Spacing and Discharge Trajectory
Bucket spacing refers to the distance between consecutive buckets on the belt or chain. It is a critical parameter that influences the elevator capacity, material pickup efficiency, and discharge characteristics. Optimal bucket spacing depends on factors such as the material properties, required throughput, and elevator speed.
Closer bucket spacing results in higher capacities but may lead to increased material spillage and component wear. Wider bucket spacing reduces the capacity but improves material pickup and discharge efficiency. Typical bucket spacing ranges from 0.5 to 2 times the bucket width, depending on the application and material properties.
Discharge trajectory refers to the path followed by the material as it exits the buckets at the elevator head. It is influenced by factors such as the bucket speed, shape, and discharge angle. Proper design of the discharge trajectory is essential for minimizing material spillage, ensuring efficient transfer to downstream equipment, and reducing dust generation
Common discharge trajectory designs include:
- Radial discharge: The material follows a circular path as it exits the buckets, suitable for free-flowing materials and high-speed elevators.
- Tangential discharge: The material follows a straight path as it exits the buckets, suitable for controlled discharge and minimizing material impact.
- Adjustable discharge: The discharge angle can be modified to suit different material properties and downstream equipment requirements.
Proper selection of bucket spacing and discharge trajectory is crucial for optimizing the elevator performance, minimizing material degradation, and ensuring efficient integration with upstream and downstream processes.
Belt and Chain Selection and Tensioning
Belt and chain selection is based on factors such as the required strength, durability, and compatibility with the material being handled. Belt selection considerations include:
- Tensile strength: The ability to withstand the tensile forces imposed by the material load and elevator height.
- Elasticity: The ability to stretch and conform to the pulley shape without permanent deformation.
- Abrasion resistance: The ability to withstand wear caused by the material and the elevator components.
- Chemical resistance: The ability to withstand degradation caused by the material or the operating environment.
Common belt materials include rubber, PVC, and polyurethane, reinforced with fabric or steel cords. Belt thickness and width are selected based on the required strength and bucket attachment method.
Chain selection considerations include
- Tensile strength: The ability to withstand the tensile forces imposed by the material load and elevator height.
- Fatigue resistance: The ability to withstand repeated loading and unloading cycles without premature failure.
- Wear resistance: The ability to withstand wear caused by the material and the elevator components.
- Corrosion resistance: The ability to withstand corrosion caused by the material or the operating environment.
Common chain types include roller chains, leaf chains, and drag chains, selected based on the application requirements and material properties. Chain pitch and breaking strength are selected based on the required capacity and elevator size.
Proper belt and chain tensioning is essential for ensuring efficient power transmission, minimizing component wear, and preventing material spillage. Tensioning methods include:
- Screw take-ups: Used for small adjustments and maintaining constant tension during operation.
- Gravity take-ups: Used for larger adjustments and accommodating belt or chain elongation over time.
- Hydraulic or pneumatic tensioners: Used for precise tensioning control and maintaining optimal tension under varying load conditions.
Proper selection and tensioning of belts and chains ensure reliable and efficient operation of the bucket elevator, minimize maintenance requirements, and extend component life.
Pulley and Shaft Design Considerations
Pulley and shaft design play a crucial role in the performance and reliability of bucket elevators. Proper selection and sizing of these components ensure efficient power transmission, minimize material spillage, and reduce component wear. Key design considerations include:
- Material of construction: Pulleys and shafts are typically made from steel or cast iron, selected based on the required strength, durability, and compatibility with the operating environment. Stainless steel or coated components may be used in corrosive or hygienic applications.
- Pulley diameter: The diameter of the head and tail pulleys is selected based on the belt or chain type, elevator speed, and required capacity. Larger diameters reduce belt or chain stress and improve power transmission efficiency but may increase the overall elevator size and cost.
- Pulley face width: The width of the pulley face is selected to match the belt or chain width and provide adequate support and traction. Insufficient face width can lead to belt or chain misalignment and increased wear.
- Shaft diameter and bearing selection: The shaft diameter is selected based on the torque and bending loads imposed by the elevator components and the material being conveyed. Proper shaft sizing ensures adequate strength and stiffness, minimizing deflection and vibration. Bearing selection is based on the shaft size, load conditions, and operating speed, with common types including ball bearings, roller bearings, and sleeve bearings.
- Lagging and crown: Pulley lagging is used to improve traction and reduce belt or chain slip, especially in high-torque or wet applications. Common lagging materials include rubber, ceramic, and polyurethane. Pulley crowning is used to keep the belt or chain centered on the pulley face, minimizing misalignment and edge wear.
- Keyways and locking elements: Keyways are used to secure the pulleys and sprockets to the shafts, transmitting the torque and preventing relative rotation. Proper keyway design and sizing are essential for ensuring reliable power transmission and preventing component failure. Locking elements, such as set screws or locking collars, are used to prevent axial movement of the components on the shaft.
Proper pulley and shaft design, combined with regular inspection and maintenance, ensure efficient and reliable operation of the bucket elevator, minimize downtime, and extend component life.
Structural Design and Support Requirements
Structural design and support requirements are critical for ensuring the stability, safety, and reliability of bucket elevator systems. The elevator structure must be designed to withstand the static and dynamic loads imposed by the conveyed material, the elevator components, and external factors such as wind and seismic activity. Key considerations include:
- Material of construction: The elevator structure is typically made from steel or aluminum, selected based on the required strength, stiffness, and corrosion resistance. In some cases, reinforced concrete or composite materials may be used for specialized applications.
- Load analysis: A comprehensive load analysis is performed to determine the forces acting on the elevator structure, including the weight of the conveyed material, the elevator components, and any external loads. The analysis considers factors such as the elevator capacity, speed, and inclination angle, as well as the material properties and environmental conditions.
- Structural configuration: The structural configuration of the elevator is selected based on the available space, required height, and integration with other equipment. Common configurations include vertical, inclined, and Z-type elevators, each with its own structural requirements and load distribution patterns.
- Bracing and support: Adequate bracing and support are essential for maintaining the structural integrity of the elevator and preventing deflection, vibration, and collapse. Bracing elements, such as trusses, ties, and cross-members, are used to distribute the loads and provide lateral stability. Support structures, such as towers, columns, and foundations, are designed to withstand the vertical loads and ensure proper alignment of the elevator components.
- Connections and fasteners: The connections between the elevator components and the support structure are designed to withstand the loads and maintain the integrity of the system. Common connection types include bolted, welded, and clamped joints, selected based on the required strength, ease of installation, and maintenance accessibility. Fastener selection is based on the load requirements, material compatibility, and environmental conditions.
- Vibration and noise control: Proper structural design and support help minimize vibration and noise generated by the elevator operation. Vibration isolation techniques, such as the use of elastomeric pads, spring isolators, or dampers, are employed to reduce the transmission of vibrations to the surrounding structure. Noise control measures, such as the use of sound-absorbing materials or enclosures, are implemented to meet the required noise level standards.
- Access and maintenance: The elevator structure is designed to provide safe and convenient access for inspection, maintenance, and repair activities. Platforms, ladders, and walkways are incorporated to allow personnel to reach critical components and perform necessary tasks. Adequate clearances and working spaces are provided around the elevator components to facilitate maintenance and minimize downtime.
Proper structural design and support, combined with regular inspection and maintenance, ensure the long-term reliability, safety, and performance of the bucket elevator system, minimizing the risk of failures and accidents.
Design Standards and Software Tools
Bucket elevator design is guided by various industry standards and regulations that ensure safety, reliability, and interoperability of the equipment. These standards provide guidelines for the design, construction, installation, and operation of bucket elevators, taking into account factors such as material properties, operating conditions, and environmental requirements. Some key standards include:
- CEMA (Conveyor Equipment Manufacturers Association) standards: CEMA provides a comprehensive set of standards for the design, manufacture, and application of conveying equipment, including bucket elevators. These standards cover topics such as safety, performance, and dimensional requirements, as well as recommendations for maintenance and troubleshooting.
- ISO (International Organization for Standardization) standards: ISO standards provide guidelines for the design, safety, and performance of continuous mechanical handling equipment, including bucket elevators. These standards cover aspects such as terminology, classification, safety requirements, and test methods.
- ATEX (ATmosphères EXplosibles) directive: The ATEX directive sets the requirements for equipment and protective systems intended for use in potentially explosive atmospheres. Bucket elevators handling combustible materials or operating in hazardous environments must comply with the ATEX directive, ensuring proper design, construction, and marking of the equipment.
- OSHA (Occupational Safety and Health Administration) regulations: OSHA regulations set the requirements for workplace safety, including the design, installation, and operation of conveying equipment. Bucket elevators must comply with OSHA regulations, ensuring the protection of workers from potential hazards such as entanglement, crushing, or falling objects.
In addition to industry standards, various software tools are available to assist in the design and analysis of bucket elevator systems. These tools help engineers and designers optimize the elevator configuration, select appropriate components, and evaluate the system performance under different operating conditions. Some common software tools include:
- CAD (Computer-Aided Design) software: CAD software, such as AutoCAD, SolidWorks, or Inventor, is used to create detailed 2D and 3D models of the bucket elevator components and assembly. These models help visualize the system layout, detect potential interferences, and generate fabrication drawings.
- FEA (Finite Element Analysis) software: FEA software, such as ANSYS or Abaqus, is used to analyze the structural behavior of the elevator components and support structure under various load conditions. FEA helps identify potential stress concentrations, deformations, and fatigue issues, allowing designers to optimize the component geometry and material selection.
- Simulation software: Simulation software, such as Discrete Element Method (DEM) tools, is used to model the behavior of the conveyed material and its interaction with the elevator components. These tools help predict the material flow patterns, power requirements, and wear characteristics, allowing designers to optimize the elevator configuration and operating parameters.
- Selection and sizing software: Many bucket elevator manufacturers provide proprietary software tools to help customers select and size the appropriate elevator components based on the application requirements. These tools typically consider factors such as material properties, capacity, lift height, and operating conditions, and provide recommendations for the bucket size and spacing, belt or chain type, and drive system.
The use of industry standards and software tools in the design and analysis of bucket elevator systems helps ensure the safety, reliability, and efficiency of the equipment, minimizing the risk of failures and optimizing the performance for the specific application requirements.
Bucket Elevator Applications and Industries
Agriculture and Grain Handling
Bucket elevators play a crucial role in the agriculture and grain handling industry, facilitating the efficient movement and storage of various agricultural products. Some common applications include:
- Grain elevators: Used for the vertical transportation of grains such as wheat, corn, soybeans, and rice from ground level to storage silos or processing equipment. Bucket elevators ensure gentle handling of the grains, minimizing damage and maintaining product quality.
- Seed processing: Used for the transportation of seeds between different stages of the cleaning, sorting, and packaging process. Bucket elevators help maintain the purity and integrity of the seeds, preventing contamination and ensuring efficient handling.
- Animal feed production: Used for the transportation of raw materials and finished feed products within the feed mill. Bucket elevators help move ingredients such as grains, pellets, and additives between storage bins, mixers, and packaging lines, ensuring consistent and efficient feed production.
Food Processing
Bucket elevators are widely used in the food processing industry for the transportation of various food products and ingredients. Some common applications include:
- Sugar processing: Used for the transportation of raw sugar, refined sugar, and sugar by-products between different stages of the production process. Bucket elevators help maintain the purity and quality of the sugar, preventing contamination and ensuring efficient handling.
- Dairy processing: Used for the transportation of powdered milk, whey, and other dairy ingredients within the processing plant. Bucket elevators help maintain the hygiene and quality of the products, preventing contamination and ensuring efficient handling.
- Cocoa and coffee processing: Used for the transportation of cocoa beans, coffee beans, and their processed products within the manufacturing plant. Bucket elevators help maintain the quality and aroma of the products, preventing damage and ensuring efficient handling.
Cement and Mining
Bucket elevators are essential for the transportation of raw materials and finished products in the cement and mining industries. Some common applications include:
- Cement production: Used for the transportation of raw materials such as limestone, clay, and clinker between different stages of the cement production process. Bucket elevators help ensure the consistent and efficient movement of materials, maintaining the quality and uniformity of the finished cement.
- Mineral processing: Used for the transportation of ores, concentrates, and tailings within the mining and mineral processing plant. Bucket elevators help move materials between crushing, grinding, and separation stages, ensuring efficient and reliable handling.
- Coal handling: Used for the transportation of coal within power plants and coal preparation facilities. Bucket elevators help move coal from storage to boilers or processing equipment, ensuring consistent and efficient fuel supply.
Chemicals and Pharmaceuticals
Bucket elevators are used in the chemical and pharmaceutical industries for the transportation of various raw materials, intermediates, and finished products. Some common applications include:
- Bulk chemical handling: Used for the transportation of bulk chemicals such as resins, pellets, and powders within the manufacturing plant. Bucket elevators help ensure the safe and efficient movement of materials, preventing contamination and maintaining product quality.
- Pharmaceutical production: Used for the transportation of raw materials, intermediates, and finished drug products within the pharmaceutical manufacturing facility. Bucket elevators help maintain the purity and integrity of the products, ensuring compliance with strict hygiene and quality standards.
- Pigment and dye production: Used for the transportation of pigments, dyes, and their raw materials within the manufacturing plant. Bucket elevators help ensure the consistent and efficient movement of materials, maintaining the quality and uniformity of the finished products.
Bulk Material Handling
Bucket elevators are widely used for the transportation of various bulk materials across different industries. Some common applications include:
- Fertilizer handling: Used for the transportation of raw materials and finished fertilizer products within the manufacturing plant. Bucket elevators help ensure the consistent and efficient movement of materials, maintaining the quality and uniformity of the finished fertilizers.
- Plastic and rubber production: Used for the transportation of plastic pellets, rubber crumbs, and other raw materials within the manufacturing facility. Bucket elevators help ensure the safe and efficient handling of materials, preventing contamination and maintaining product quality.
- Wood and biomass processing: Used for the transportation of wood chips, sawdust, and other biomass materials within the processing plant. Bucket elevators help ensure the consistent and efficient movement of materials, facilitating the production of wood-based products or biofuels.
The versatility and reliability of bucket elevators make them essential equipment for the efficient handling and transportation of bulk materials across a wide range of industries and applications.
Bucket Elevator Installation, Operation, and Maintenance
Proper installation, operation, and maintenance of bucket elevators are crucial for ensuring safe, efficient, and reliable performance. Follow these best practices to optimize the longevity and productivity of your bucket elevator system.
Installation Procedures and Guidelines
- Carefully review the manufacturer’s installation manual and drawings before starting the installation process.
- Ensure that the installation site is properly prepared, with a level and stable foundation, adequate clearances, and necessary utilities.
- Assemble the bucket elevator components according to the manufacturer’s instructions, paying close attention to the alignment and orientation of the parts.
- Use appropriate lifting and handling equipment to safely move and position the bucket elevator components during installation.
- Properly secure the bucket elevator to the foundation and support structures, using the specified anchors and fasteners.
- Connect the electrical and control systems according to the manufacturer’s wiring diagrams and applicable codes and standards.
- Install appropriate safety devices, such as emergency stop switches, guards, and interlocks, to ensure operator safety and compliance with regulations.
Commissioning and Testing
- Conduct a thorough visual inspection of the installed bucket elevator to ensure that all components are properly assembled and secured.
- Check the alignment and tension of the belt or chain, making necessary adjustments according to the manufacturer’s specifications.
- Lubricate the bearings, chains, and other moving parts as specified in the maintenance manual.
- Test the operation of the bucket elevator at various speeds and load conditions to verify proper functioning and performance.
- Monitor the current draw and temperature of the motor and gearbox to ensure they are within the acceptable ranges.
- Verify the proper functioning of safety devices, such as emergency stop switches, guards, and interlocks.
- Document the commissioning and testing results, and address any issues or discrepancies before putting the bucket elevator into service.
Operational Best Practices and Safety Considerations
- Train operators on the proper use, safety precautions, and emergency procedures for the bucket elevator.
- Ensure that the bucket elevator is operated within its designed capacity and speed range to prevent overloading and excessive wear.
- Monitor the material flow and loading conditions to ensure consistent and efficient operation, making adjustments as necessary.
- Regularly inspect the bucket elevator for signs of wear, damage, or malfunction, such as unusual noises, vibrations, or material spillage.
- Keep the area around the bucket elevator clean and free of debris to prevent interference with the moving parts and reduce the risk of fire or explosion.
- Implement appropriate lockout/tagout procedures during maintenance or repair activities to prevent accidental start-up and ensure worker safety.
- Use appropriate personal protective equipment (PPE), such as hard hats, safety glasses, and gloves, when working around the bucket elevator.
- Comply with applicable safety regulations and standards, such as OSHA and ATEX, to ensure a safe working environment and minimize the risk of accidents.
Preventive Maintenance and Troubleshooting
- Establish a regular preventive maintenance schedule based on the manufacturer’s recommendations and the specific operating conditions.
- Conduct routine inspections of the bucket elevator components, such as buckets, belts, chains, bearings, and pulleys, to identify and address any wear, damage, or misalignment.
- Lubricate the moving parts, such as bearings and chains, according to the manufacturer’s specifications to reduce friction and extend their service life.
- Clean the bucket elevator regularly to remove any accumulated material, dust, or debris that can interfere with its operation or cause contamination.
- Monitor the performance of the bucket elevator, such as speed, capacity, and power consumption, to identify any deviations from the normal operating parameters.
- Troubleshoot any issues or malfunctions promptly, using the manufacturer’s troubleshooting guide or seeking assistance from qualified technicians.
- Keep a record of all maintenance activities, repairs, and replacements to track the performance and condition of the bucket elevator over time.
- Stock commonly used spare parts and consumables to minimize downtime and ensure quick repairs in case of breakdowns.
By following these installation, operation, and maintenance best practices, you can ensure the safe, efficient, and reliable performance of your bucket elevator system, maximizing its productivity and longevity.
Bucket Elevator Selection and Customization
Selecting the right bucket elevator for your specific application is crucial for ensuring optimal performance, efficiency, and reliability. Consider the following factors when choosing a bucket elevator:
Material Characteristics
- Particle size and shape: Select a bucket elevator that can handle the size and shape of the material being conveyed, ensuring proper loading and discharge.
- Bulk density: Consider the bulk density of the material to determine the required bucket size and spacing for optimal capacity and efficiency.
- Flowability: Evaluate the flowability of the material to select a bucket elevator that can handle the material’s flow characteristics, such as cohesiveness or tendency to stick.
- Abrasiveness: Choose a bucket elevator with appropriate materials and coatings to withstand the abrasive nature of the material being conveyed, minimizing wear and tear.
- Moisture content: Consider the moisture content of the material and select a bucket elevator that can handle the specific conditions, such as corrosion resistance or drainage requirements.
Capacity and Throughput
- Desired capacity: Determine the required throughput of the bucket elevator in terms of volume or weight per unit time to select a model with adequate size and speed.
- Peak demands: Consider any peak demand periods or fluctuations in the material flow to ensure that the bucket elevator can handle the maximum capacity requirements.
- Future growth: Select a bucket elevator with sufficient capacity to accommodate any anticipated future growth or expansion in production.
Elevation and Conveying Distance
- Lifting height: Determine the required lifting height of the bucket elevator based on the facility layout and equipment arrangement.
- Horizontal conveying distance: Consider the horizontal conveying distance, if any, to select a bucket elevator configuration that can efficiently transfer the material between the desired points.
- Incline or vertical angles: Evaluate the required incline or vertical angles of the bucket elevator to ensure proper material loading and discharge.
Space and Layout Constraints
- Available floor space: Consider the available floor space and layout of the facility to select a bucket elevator configuration that can fit within the designated area.
- Headroom clearance: Ensure that the selected bucket elevator has sufficient headroom clearance for installation, operation, and maintenance.
- Integration with other equipment: Evaluate how the bucket elevator will integrate with other material handling equipment, such as conveyors, silos, or processing machines, to ensure smooth material flow and compatibility.
Operational and Environmental Factors
- Operating temperature: Select a bucket elevator that can withstand the expected operating temperature range, considering any heat generated by the material or the surrounding environment.
- Humidity and moisture: Choose a bucket elevator with appropriate corrosion resistance and sealing to handle the expected humidity and moisture levels in the operating environment.
- Dust and contamination: Consider any dust or contamination control requirements and select a bucket elevator with appropriate enclosures, seals, or dust collection systems.
- Noise and vibration: Evaluate the noise and vibration levels of the bucket elevator and select a model that meets the required standards and regulations for the specific application and environment.
Maintenance and Serviceability
- Ease of maintenance: Select a bucket elevator with a design that facilitates easy access to critical components for inspection, lubrication, and replacement.
- Spare parts availability: Consider the availability and lead time of spare parts to minimize downtime and ensure quick repairs in case of breakdowns.
- Service and support: Evaluate the level of service and technical support provided by the manufacturer, including documentation, training, and on-site assistance.
Customization Options
Bucket elevators can be customized to meet specific application requirements. Some common customization options include:
- Material of construction: Select the appropriate material of construction for the buckets, casing, and other components to suit the specific material being handled and the operating environment.
- Bucket design and spacing: Customize the bucket design, size, and spacing to optimize the loading and discharge of the specific material being conveyed.
- Drive and control systems: Select the appropriate drive system, such as motor, gearbox, and variable frequency drive (VFD), to meet the specific power and speed requirements of the application.
- Safety and monitoring devices: Incorporate additional safety features, such as emergency stop switches, overload protection, or belt misalignment sensors, to enhance the safety and reliability of the bucket elevator.
- Dust control and containment: Customize the bucket elevator with dust-tight enclosures, seals, or dust collection systems to minimize dust generation and ensure a clean and safe working environment.
- Material feeding and discharge: Customize the feeding and discharge arrangements, such as hoppers, chutes, or valves, to ensure efficient material flow and minimize spillage or contamination.
By carefully evaluating these selection criteria and considering the available customization options, you can choose a bucket elevator that is optimally suited for your specific application, ensuring efficient, reliable, and cost-effective material handling.
Bucket Elevator Standards and Regulations
Bucket elevators are subject to various standards and regulations to ensure safe, reliable, and efficient operation. These standards and regulations cover aspects such as design, construction, installation, and maintenance of bucket elevators, as well as safety and environmental considerations. Some of the key standards and regulations include:
International and Regional Standards
- ISO 21873-1: Bucket elevators for bulk materials – Part 1: Bucket elevators for agricultural and food products
- ISO 21873-2: Bucket elevators for bulk materials – Part 2: Bucket elevators for industrial use
- EN 618: Continuous handling equipment and systems – Safety and EMC requirements for equipment for mechanical handling of bulk materials except fixed belt conveyors
- EN 619: Continuous handling equipment and systems – Safety and EMC requirements for equipment for mechanical handling of unit loads
- ANSI/CEMA 300: Screw Conveyors, Bucket Elevators, and Bulk Material Handling Equipment
These standards provide guidelines for the design, construction, and testing of bucket elevators to ensure their safe and efficient operation. They cover aspects such as material selection, bucket design, belting, drives, safety devices, and electrical requirements.
Safety Regulations and Guidelines
- OSHA 1910.272: Grain handling facilities
- OSHA 1910.269: Electric power generation, transmission, and distribution
- OSHA 1926.555: Conveyors
- NFPA 61: Standard for the Prevention of Fires and Dust Explosions in Agricultural and Food Processing Facilities
- NFPA 652: Standard on the Fundamentals of Combustible Dust
These regulations and guidelines aim to protect workers from potential hazards associated with bucket elevators, such as entanglement, falls, electrical hazards, and dust explosions. They specify requirements for guarding, emergency stop devices, lockout/tagout procedures, and dust control measures.
Environmental Regulations
- EPA Clean Air Act: Regulates air emissions from industrial facilities, including dust and particulate matter generated by bucket elevators.
- EPA Resource Conservation and Recovery Act (RCRA): Regulates the handling, storage, and disposal of hazardous and non-hazardous solid waste, which may be relevant for bucket elevators handling certain materials.
- EU Directive 2006/42/EC: Machinery Directive, which sets out the essential health and safety requirements for machinery, including bucket elevators.
- EU Directive 2014/34/EU: ATEX Directive, which covers equipment and protective systems intended for use in potentially explosive atmospheres.
These regulations aim to minimize the environmental impact of bucket elevators by controlling dust emissions, preventing contamination, and ensuring proper waste management. They also specify requirements for the safe operation of bucket elevators in potentially explosive atmospheres.
Certification and Testing Requirements
Many industries and jurisdictions require bucket elevators to undergo specific certification and testing procedures to ensure compliance with the relevant standards and regulations. Some common certification and testing requirements include:
- CE Marking: Mandatory for bucket elevators sold within the European Economic Area (EEA), indicating compliance with the applicable EU directives.
- UL Listing: Voluntary certification for bucket elevators, demonstrating compliance with UL safety standards.
- ATEX Certification: Required for bucket elevators operating in potentially explosive atmospheres, ensuring compliance with the ATEX directive.
- Factory Acceptance Testing (FAT): Conducted at the manufacturer’s facility to verify the performance and safety of the bucket elevator before shipment.
- Site Acceptance Testing (SAT): Conducted at the installation site to ensure proper functioning and safety of the bucket elevator after installation.
Compliance with these standards and regulations is essential for ensuring the safe, reliable, and efficient operation of bucket elevators while minimizing risks to workers, the environment, and the general public. Manufacturers, installers, and operators of bucket elevators must stay informed about the applicable standards and regulations and ensure ongoing compliance through regular inspections, maintenance, and training.
In summary, bucket elevators are subject to a range of international and regional standards, safety regulations, environmental regulations, and certification and testing requirements. These standards and regulations cover various aspects of bucket elevator design, construction, installation, operation, and maintenance to ensure safe, reliable, and efficient material handling while minimizing risks to workers, the environment, and the general public.
Elevator Bucket Trucks for Sale
Elevator bucket trucks are essential for various aerial work applications, providing a safe and efficient means of reaching high elevations. When looking for an elevator bucket truck for sale, consider factors such as the working height, bucket capacity, and truck specifications. Popular brands like Altec and Aseeco offer a range of elevator bucket trucks to suit different needs.
For example, a 75-foot elevator bucket truck provides a generous working height for tasks such as utility maintenance, tree trimming, and construction work. Rear-mount elevator bucket trucks offer excellent stability and maneuverability, making them ideal for work in tight spaces. Before purchasing an elevator bucket truck, ensure that it meets all the necessary safety standards and regulations, and consider the availability of spare parts and service support.
Bucket Elevator Chain and Belt Selection
The chain and belt are critical components of a bucket elevator, responsible for carrying the buckets and transmitting power. When selecting a bucket elevator chain, consider factors such as the chain pitch, breaking strength, and material of construction. Common chain types include forged link chains, which offer high strength and durability, and manufactured link chains, which provide a cost-effective solution for lighter-duty applications.
Bucket elevator belts, on the other hand, are typically made from materials such as rubber, PVC, or polyurethane, reinforced with fabric or steel cords. Belt selection depends on factors such as the required tensile strength, bucket attachment method, and the material being conveyed. Proper chain and belt selection, along with regular inspection and maintenance, ensure the reliable and efficient operation of the bucket elevator.
Bucket Elevator Capacity Calculation
Calculating the capacity of a bucket elevator is crucial for ensuring that it meets the required material handling throughput. The capacity of a bucket elevator depends on various factors, such as the bucket size, spacing, speed, and fill factor. To calculate the bucket elevator capacity, use the following formula:
Capacity (m³/h) = Bucket Volume (m³) × Bucket Spacing (m) × Speed (m/s) × Fill Factor × 3600
The bucket volume can be obtained from the manufacturer’s catalogue or calculated based on the bucket dimensions. The fill factor represents the percentage of the bucket volume that is actually filled with material, typically ranging from 0.6 to 0.8. The speed of the bucket elevator is determined based on the required capacity and the material properties, with typical speeds ranging from 0.5 to 2 m/s. It’s essential to consider the material properties, such as bulk density and flowability, when selecting the appropriate bucket size and spacing to achieve the desired capacity. Online bucket elevator capacity calculators and spreadsheet tools (XLS) can assist in performing these calculations quickly and accurately.
Bucket Elevator Design Calculation and Troubleshooting
Proper bucket elevator design involves careful consideration of various factors, such as the material properties, required capacity, lift height, and power requirements. Key design calculations include the determination of the chain or belt tension, bucket spacing, drive power, and discharge trajectory.
The chain or belt tension is calculated based on the material load, lift height, and the chain or belt weight, while the drive power is determined based on the required lifting force and the efficiency of the drive system. Bucket spacing and discharge trajectory are optimized to ensure efficient material pickup and discharge, minimizing spillage and wear. Detailed design calculations are typically performed using spreadsheet tools (XLS) or specialized software, taking into account the relevant standards and design codes.
When troubleshooting bucket elevator problems, it’s essential to have a comprehensive understanding of the system’s working principle and the potential failure modes. Common issues include chain or belt misalignment, excessive wear, material spillage, and drive system failures. A systematic troubleshooting procedure should be followed, starting with a visual inspection of the equipment, followed by an analysis of the operating parameters and the material flow. Consulting the manufacturer’s troubleshooting guide and maintenance manuals can provide valuable guidance in identifying and rectifying problems. Regular preventive maintenance, including lubrication, tension adjustment, and worn component replacement, can help prevent many common bucket elevator issues.
Z-Type Bucket Elevators and Other Configurations
Z-type bucket elevators, also known as zig-zag or inclined elevators, are a popular configuration for handling materials that tend to slide or roll back, such as sand, gravel, or fertilizers. In a Z-type elevator, the buckets are attached to a chain or belt that follows a Z-shaped path, with intermediate pulleys to change the direction of travel.
This configuration allows for a more compact design compared to vertical elevators, while still providing efficient material handling. Other bucket elevator configurations include the Aumund central chain design, which features a single chain running through the center of the buckets, providing a balanced and stable operation.
Continuous discharge elevators, such as those offered by Bühler and GSI, are designed for gentle handling of fragile materials like grains and seeds. Mobile and portable bucket elevators, such as those manufactured by Martin and Mini, offer flexibility for temporary or multi-site applications.
When selecting a bucket elevator configuration, consider factors such as the material properties, available space, and integration with other equipment. Manufacturers like Aumund, Bühler, and GSI offer comprehensive catalogs and technical specifications to help in the selection process. Specialized bucket elevator designs, such as the Honeyville drum elevator or the Aseeco pendulum bucket conveyor, cater to specific material handling requirements. Ultimately, the choice of bucket elevator configuration depends on a thorough understanding of the application requirements and a careful evaluation of the available options.
Calculating Bucket Elevator Capacity
To calculate bucket elevator capacity, use this formula:
Capacity (m³/h) = Bucket Volume (m³) × Bucket Spacing (m) × Speed (m/s) × Fill Factor × 3600
Where bucket volume is the volume of a single bucket, bucket spacing is the distance between buckets, speed is the linear speed of the belt or chain, and fill factor is the percentage of bucket volume filled with material (usually 0.6-0.8). Multiply the result by material bulk density (t/m³) for capacity in tons per hour (t/h).
How Bucket Elevators Work
A bucket elevator works by using a continuous loop of buckets attached to a belt or chain to convey material vertically:
- Material is fed into the boot section, where buckets scoop it up.
- Buckets carry the material vertically along the casing.
- At the head pulley, buckets discharge the material by gravity or centrifugal force.
- Empty buckets return to the boot section to repeat the cycle.
- A motor and gearbox drive the head pulley, which powers the belt or chain.
Bucket elevators efficiently convey various bulk materials to significant heights in industries such as agriculture, food processing, and mining.
Bucket Elevator Maintenance Checklist
A comprehensive maintenance checklist is essential for ensuring the reliable and efficient operation of bucket elevators. The checklist should include items such as:
- Inspecting the belt or chain for wear, damage, and proper tension
- Checking the buckets for cracks, holes, or excessive wear
- Lubricating bearings and other moving parts
- Cleaning the boot section and ensuring proper material flow
- Verifying the alignment of the belt or chain and adjusting the tracking if necessary
- Testing safety devices such as switches, interlocks, and overload protection
- Measuring the bucket elevator’s horsepower and RPM to ensure optimal performance
Regular maintenance based on a comprehensive checklist can help prevent unexpected downtime, prolong equipment life, and ensure a safe working environment.
Bucket Elevator Components and Accessories
In addition to the main components like buckets, belts, and chains, bucket elevators rely on various accessories and parts to function efficiently. These include:
- Elevator bolts and cups for securely attaching buckets to the belt or chain
- Splice kits and fasteners for joining belt or chain ends
- Take-up devices for maintaining proper belt or chain tension and tracking
- Backstops and brakes for preventing reverse rotation and ensuring safe operation
- Loading hoppers and inlet chutes for controlled material feeding
- Discharge spouts and valves for directing material flow
- Inspection doors and access platforms for easy maintenance and monitoring
Selecting high-quality, compatible components and accessories is crucial for the optimal performance and longevity of bucket elevators.
The Importance Of Bucket Elevator Specifications and Drawings
Detailed specifications and drawings are essential for the proper design, installation, and maintenance of bucket elevators. Key information typically includes:
- Elevator layout and dimensions, including lift height and center distances
- Material specifications for buckets, belts, chains, and casing
- Drive system details, including motor horsepower, gearbox ratio, and RPM
- Loading and discharge arrangements, such as hopper dimensions and chute angles
- Safety device specifications, such as switches, sensors, and guards
- Capacity and speed ratings, along with any limiting factors
- Foundation and support structure requirements
Drawings may be provided in various formats, such as DWG (AutoCAD), PDF, or GIF, to facilitate communication between stakeholders and ensure accurate installation and maintenance.
Bucket Elevator Selection and Customization
Choosing the right bucket elevator for a specific application involves considering factors such as:
- Material properties, including particle size, density, and flowability
- Required capacity and throughput rates
- Elevation height and conveying distance
- Available space and layout constraints
- Environmental conditions, such as temperature, humidity, and corrosiveness
- Integration with other equipment and processes
- Maintenance and service requirements
By understanding the unique requirements of each application and working closely with experienced suppliers, facility managers can select and customize bucket elevators that deliver optimal performance, reliability, and value for their specific needs.
Bucket Elevator Pricing and Specifications
When considering the price of a bucket elevator, it’s essential to review the detailed specifications and drawings provided by the manufacturer. A specification sheet typically includes information such as the elevator’s capacity, dimensions, power requirements, and materials of construction. Comparing specifications and prices from multiple distributors can help you make an informed decision when looking to buy a bucket elevator that meets your specific needs.
Bucket Elevator Components and Measurements
A bucket elevator consists of several key components, including the buckets, belt or chain, drive system, and supporting structure or tower. The buckets are attached to the belt or chain at regular intervals, determined by the required capacity and material properties. The belt or chain is driven by a motor and gearbox, which are selected based on the required power and speed. Accurate measurements of the elevator’s dimensions, such as the center distance between the head and tail pulleys, are crucial for proper installation and integration with other equipment.
Bucket Elevator Belts and Joints
The belt is a critical component of belt-driven bucket elevators, responsible for carrying the buckets and transmitting power. Belts are typically made from materials such as rubber, PVC, or polyurethane, and may be reinforced with fabric or steel cords for added strength. The joint or splice where the belt ends are connected is a potential weak point and must be designed and installed correctly to ensure reliable operation. Factors such as belt thickness, width, and ply construction are specified based on the application requirements and the manufacturer’s recommendations.
Bucket Elevator Safety and Monitoring
Ensuring the safe operation of bucket elevators is crucial for protecting workers and preventing accidents. Safety features such as guards, emergency stop switches, and overload protection devices are essential for mitigating risks associated with moving parts and potential blockages. Monitoring systems, such as belt alignment sensors and speed switches, can help detect issues early and prevent damage or downtime. Platforms and access ladders should be provided for safe maintenance and inspection activities.
Bucket Elevator Applications and Industries
Bucket elevators find applications across a wide range of industries, from agriculture and food processing to mining and construction. In the forestry industry, for example, bucket elevators are used for handling wood chips and biomass materials. Other common applications include grain handling, cement production, and bulk material storage in silos. The versatility and reliability of bucket elevators make them a popular choice for vertical conveying in many industrial settings.
Bucket Elevator Design and Animation
Proper bucket elevator design involves considering factors such as the material properties, required capacity, and elevation height. Engineers use specialized software to create detailed drawings and 3D models of the elevator, including the buckets, casing, and drive system. Animation tools can be used to simulate the operation of the elevator and identify potential issues or areas for improvement. Design calculations, such as those for power requirements and belt tensions, are typically performed using spreadsheets or calculators based on industry standards and best practices.
Bucket Elevator Troubleshooting and Maintenance
Regular maintenance and timely troubleshooting are essential for ensuring the reliable and efficient operation of bucket elevators. Common issues include belt or chain misalignment, excessive wear, and material buildup. Symptoms such as unusual noises, vibrations, or reduced capacity can indicate potential problems that require attention. Maintenance activities, such as lubrication, belt tensioning, and bucket replacement, should be performed according to the manufacturer’s recommendations and industry best practices. Proper maintenance can help extend the life of the equipment and prevent costly downtime.
Bucket Elevator Market and Innovation
The global bucket elevator market is driven by factors such as increasing industrialization, growing demand for bulk material handling, and the need for efficient and reliable conveying solutions. Manufacturers are continually developing new technologies and designs to improve the performance and efficiency of bucket elevators. Innovations such as the use of high-strength materials, modular designs, and advanced control systems are helping to meet the evolving needs of various industries. As the market continues to grow, it is essential for suppliers to stay up-to-date with the latest trends and customer requirements to remain competitive.
Bucket Elevator Calculator
A bucket elevator calculator is a useful tool for designing and selecting the appropriate elevator for a specific application. The calculator typically takes into account factors such as the required capacity, material properties, and elevator dimensions to determine the optimal bucket size, spacing, and speed. Some calculators also provide information on power requirements and belt or chain tensions. Using a bucket elevator calculator can save time and ensure accurate sizing, reducing the risk of performance issues or equipment failure.
Elevator Bucket Size Chart
An elevator bucket size chart is a tabular representation of the available bucket sizes and their corresponding capacities for a specific bucket elevator model or manufacturer. The chart typically includes information such as the bucket width, height, and capacity in terms of volume or weight. Some charts may also provide recommendations for bucket spacing and belt or chain speed based on the material being handled. Using an elevator bucket size chart can help in selecting the appropriate bucket size for a given application, ensuring optimal capacity and performance.
Bucket Elevator Platform
A bucket elevator platform is a structural component that provides support and access for maintenance and inspection activities. Platforms are typically located at strategic points along the elevator, such as near the head or tail pulleys, or at intermediate points for taller elevators. They provide a safe and stable surface for workers to stand on while performing tasks such as lubrication, belt or chain tensioning, or bucket replacement. Bucket elevator platforms are designed to withstand the loads and vibrations generated by the elevator and are typically equipped with safety features such as guardrails and toe boards.
Bucket Elevator Chain Elongation Measurement
Bucket elevator chain elongation measurement is a critical maintenance activity that involves monitoring the length of the chain over time to detect wear and stretching. As the chain is subjected to tension and wear, it gradually elongates, which can cause performance issues and potentially lead to failure if not addressed. Chain elongation is typically measured using a specialized tool or gauge that compares the current length of the chain to its original length. Regular chain elongation measurements can help identify when the chain needs to be adjusted, repaired, or replaced, ensuring optimal performance and safety.
Bucket Elevator Diagram
A bucket elevator diagram is a visual representation of the key components and arrangement of a bucket elevator system. The diagram typically includes the buckets, belt or chain, pulleys, drive system, and supporting structures, as well as any feeding or discharge components. Bucket elevator diagrams can be in the form of 2D drawings or 3D models and are used for various purposes, such as design, installation, maintenance, and troubleshooting. They provide a clear and concise way to communicate the layout and function of the elevator to stakeholders, such as engineers, operators, and maintenance personnel.
Positive Discharge Bucket Elevator
A positive discharge bucket elevator is a type of elevator designed to ensure complete and controlled discharge of the material at the outlet point. In a positive discharge system, the buckets are typically mounted on a chain and equipped with a mechanism that forcibly ejects the material from the bucket as it passes over the head pulley. This mechanism can be in the form of a striker plate, a cam, or a pivoting bucket design. Positive discharge bucket elevators are particularly useful for handling materials that tend to stick or clump, ensuring efficient and reliable discharge without spillage or carryover.
Traction Wheel for Bucket Elevator
A traction wheel, also known as a friction wheel or a lagged pulley, is a specialized component used in bucket elevators to improve the grip and reduce slip between the belt or chain and the drive pulley. Traction wheels are typically made from materials such as rubber, polyurethane, or ceramic, which provide a high-friction surface that grips the belt or chain. The increased traction helps to prevent slippage and improves the efficiency of power transmission, particularly in applications with high loads or wet conditions. Traction wheels are often used in conjunction with tensioning devices to maintain optimal belt or chain tension and alignment.
Belt Sway Switch for Bucket Elevator
A belt sway switch, also known as a misalignment switch or a belt tracking switch, is a safety device used to detect excessive lateral movement or misalignment of the belt in a bucket elevator. The switch is typically mounted on the casing near the head or tail pulley and consists of a pair of sensors or paddles that are activated when the belt sways beyond a preset limit. When activated, the switch sends a signal to the control system, which can trigger an alarm, shut down the elevator, or initiate a corrective action. Belt sway switches help to prevent damage to the belt, buckets, and other components, as well as reduce the risk of spillage and contamination.
Glossary Of Terms
- Bucket: A container attached to a belt or chain that carries the material being conveyed in a bucket elevator.
- Belt: A continuous, flexible strip made of fabric, rubber, or plastic that carries the buckets and transfers power in a belt-driven bucket elevator.
- Chain: A series of interconnected metal links that carry the buckets and transfer power in a chain-driven bucket elevator.
- Head pulley: The pulley located at the top of the bucket elevator that drives the belt or chain and is connected to the motor and gearbox.
- Tail pulley: The pulley located at the bottom of the bucket elevator that maintains tension on the belt or chain and guides its return.
- Boot: The lower section of the bucket elevator housing where the buckets are loaded with material.
- Discharge: The point at which the material is unloaded from the buckets at the top of the elevator.
- Casing: The enclosure that surrounds the bucket elevator and contains the material being conveyed.
- Takeup: A device that maintains proper tension on the belt or chain to ensure efficient power transmission and prevent slippage.
- Backstop: A device that prevents the backward rotation of the bucket elevator, protecting the drive components and ensuring safe operation.
- Capacity: The maximum volume or weight of material that a bucket elevator can convey per unit time, typically expressed in cubic meters per hour (m³/h) or tons per hour (t/h).
- Lift height: The vertical distance between the boot and the discharge point of the bucket elevator.
- Speed: The linear velocity of the belt or chain, typically expressed in meters per second (m/s) or feet per minute (ft/min).
- Spacing: The distance between consecutive buckets on the belt or chain.
- Fill factor: The ratio of the actual volume of material in the bucket to the theoretical volume of the bucket, expressed as a percentage.
- Centrifugal discharge: A type of bucket elevator discharge where the material is thrown out of the buckets by centrifugal force at the head pulley.
- Continuous discharge: A type of bucket elevator discharge where the material is discharged continuously as the buckets pass over the head pulley.
- Spillage: The loss of material from the buckets or the transfer points, which can cause contamination and reduce efficiency.
- Elevator leg: The vertical section of the bucket elevator that contains the buckets and the belt or chain.
- Turnhead: A component at the top of the elevator that changes the direction of the material flow from vertical to horizontal.
- Trunking: The horizontal sections of the casing that connect the elevator leg to the boot and the discharge.
- Drive: The system that powers the bucket elevator, typically consisting of a motor, gearbox, and coupling.
- Elevator capacity: The maximum volume or weight of material that a bucket elevator can convey per unit time, typically expressed in cubic meters per hour (m³/h) or tons per hour (t/h).
- Tensile strength: The maximum stress that a material (such as a belt or chain) can withstand before breaking, typically expressed in Newtons (N) or pounds-force (lbf).
- Bucket density: The ratio of the total volume of the buckets to the total volume of the casing, expressed as a percentage.
- Bucket projection: The distance that the buckets extend beyond the edge of the belt or chain.
- Welded steel bucket: A type of bucket made from steel plates welded together to form a strong, rigid container.
- Plastic bucket: A type of bucket made from lightweight, corrosion-resistant plastic materials such as polyethylene or polypropylene.
- Continuous bucket: A type of bucket designed for gentle handling of fragile materials, with overlapping or interlocking edges to minimize spillage.
- Pivoted bucket: A type of bucket that is attached to the belt or chain by a pivot pin, allowing it to swing freely and discharge material more effectively.
- Bucket bolt: A fastener used to attach the bucket to the belt or chain, typically made of steel or stainless steel.
- Elevator boot: The lower section of the bucket elevator housing where the buckets are loaded with material.
- Boot pulley: The pulley located in the boot section of the bucket elevator that guides the return of the belt or chain.
- Bucket scraper: A device used to clean the buckets and prevent material buildup, typically made of rubber or plastic.
- Elevator casing: The enclosure that surrounds the bucket elevator and contains the material being conveyed.
- Casing liner: A removable lining inside the casing that protects it from wear and corrosion, typically made of abrasion-resistant materials such as steel or polyurethane.
- Inspection door: An opening in the casing that allows access to the interior of the bucket elevator for inspection and maintenance.
- Explosion vent: A safety device that relieves pressure in the event of a dust explosion inside the bucket elevator, typically consisting of a burst panel or rupture disc.
- Dust collection: A system that captures and removes dust generated during the operation of the bucket elevator, typically consisting of hoods, ducts, and filters.
- Overload protection: A safety device that shuts down the bucket elevator in case of an overload or blockage, typically consisting of a shear pin or an electronic load monitor.
These terms cover the main components, features, and concepts related to bucket elevators. Understanding these terms is essential for effective communication, operation, and maintenance of bucket elevator systems.
What is a bucket elevator?
A bucket elevator is a vertical conveying system that uses a series of buckets attached to a belt or chain to transport bulk materials upward. It’s commonly used in industries like agriculture, mining, and manufacturing for efficient vertical material handling.
What are alternatives to the bucket elevator?
The main alternatives to bucket elevators are pneumatic conveyor systems, which uses compressed air to move materials through enclosed pipes, and screw conveyors, which push product through a tube with an auger. These systems are especially effective for lightweight materials and situations requiring enclosed transport.
What is the difference between centrifugal and continuous bucket elevators?
Centrifugal bucket elevators discharge materials using rotational force at high speeds, while continuous bucket elevators use closely-spaced buckets for gradual discharge. The key difference lies in their discharge method and material handling capabilities.
What is the formula for a bucket elevator?
The bucket elevator capacity formula is Q = 3.6 × v × γ × i × ψ, where v is belt speed (m/s), γ is material density (kg/m³), i is bucket volume (m³), and ψ is filling efficiency (typically 0.7-0.8).