- Vertical Conveyor Overview
Ryson is the number one manufacturer of Spiral Vertical Conveyors in the USA.
A Vertical Conveyor from Ryson needs less floor space than conventional incline conveyors and are also faster and more reliable than any elevator or lift. Central to our design is the proprietary slat-type belts with rolling friction and without any sliding movements or wear-strips.
Ryson Spiral Vertical Conveyors are based on an innovative modular technology, offering many features and benefits.
All Ryson Spiral Conveyors are made to order and comes in a wide range of sizes and configurations. Our proprietary modular design allows Ryson to customize with ease and to modify in the field to accommodate emerging needs.
- Gallery
- Vertical Conveyor Features & Benefits
Ryson Spiral Conveyors have many unique features that make them ideal Vertical Conveyor Solutions. Many of our features are designed to save money in the long term, essentially lowering your total cost of ownership.
Design Flexibility: Our unique vertical conveyor design offers flexibility of configuration. It also adds the ability to field modify our vertical conveyors to accommodate changing future needs at a fraction of the cost of a new conveyor.
Overlapping slats provide a smooth and efficient conveying surface, ensuring gentle product handling and suitable for all types of conveyable items. Our efficient rolling friction chain-slat design only needs a single drive, resulting in substantial savings in energy, controls and systems integration.
Our innovative chain-slat design enables a low friction operation without any sliding movements or wear-strips. This allows the Spiral to stop and start fully loaded.
Our efficient rolling friction chain-slat design only needs a single drive, resulting in substantial savings in energy, controls and systems integration.
Most Spirals ship in one piece and leave our factory pre-assembled and pre-tested. Installation is generally an efficient process and reduces time for implantation and integration.
Vertical Conveying saves space. Our spiral convey vertically within a very small footprint which is beneficial to reduce production space needed in a new facility and also to replace existing equipment in a very tight layout.
Our Vertical Conveyors and components are designed for reliability, low maintenance and long life. They have an impressive up-time record reducing the total cost of ownership.
Click below to read details about more of our features:
A quick comparison
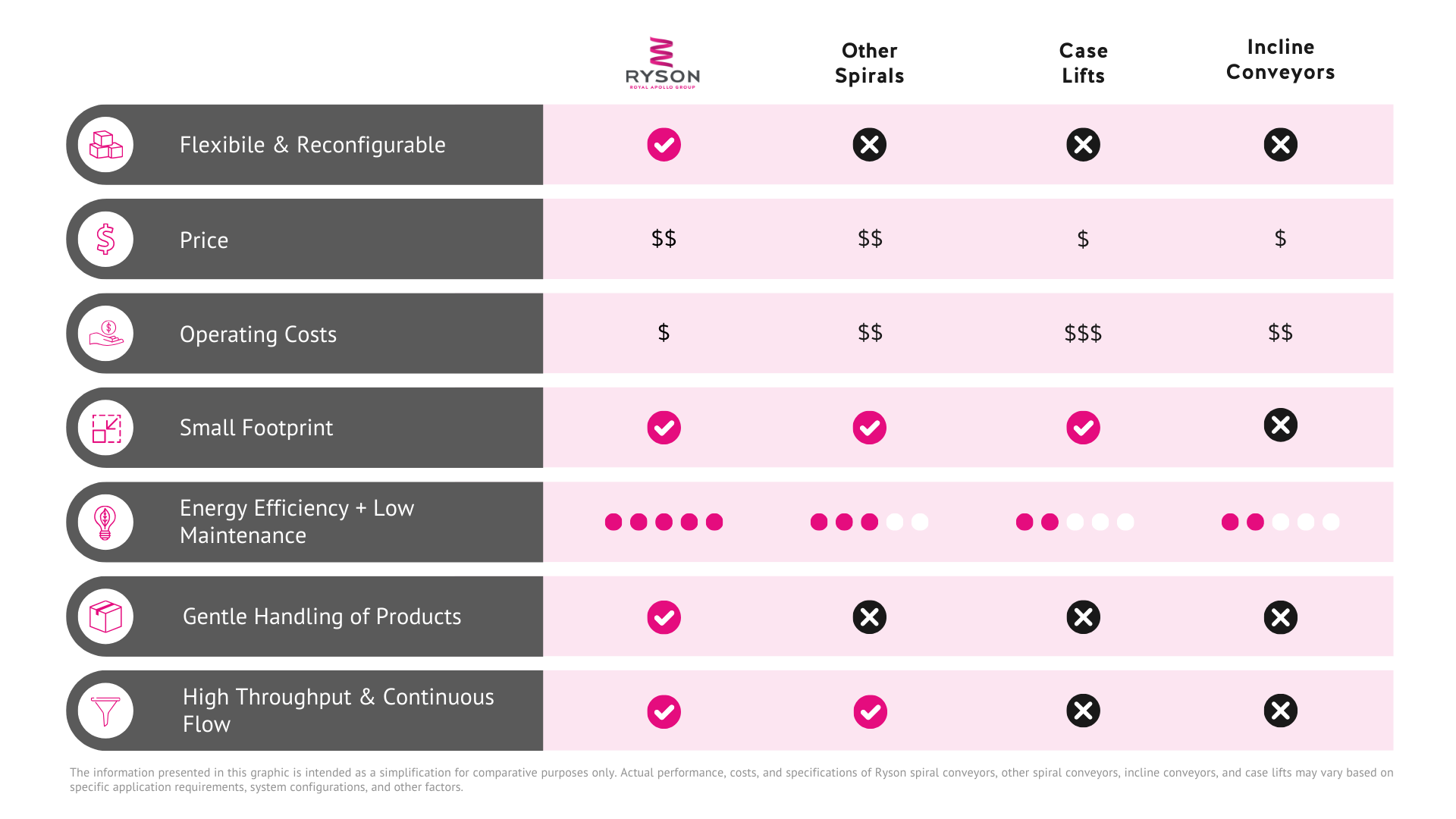
Ryson Spiral Conveyors lead the way with unmatched flexibility, compact design, and energy efficiency. This makes them the top choice for operations focusing on a high throughput and continuous flow.
Unlike lifts or incline conveyors, which can be limited by space, maintenance needs, or stop-and-go movement, Ryson Spirals handle products gently while maintaining low operating costs over time.
For facilities needing adaptable, efficient, and space-saving solutions, Ryson Spirals are a smart, long-term investment.
The Spiral Conveyors convey loads up or down in a continuous flow, facilitating high throughput. Many spirals can operate at speeds in excess of 200 FPM and are optionally reversible.
Only one drive motor is required for our vertical conveyor, resulting in substantial savings in energy, controls and systems integration.
All Ryson Vertical Spiral Conveyors are made to order and come in a wide range of sizes and configurations.
Ryson Vertical Conveyors are designed for low maintenance and long life. Only high quality components are used throughout. All bearings are sealed for life and need no further lubrication. The chain is of heavy duty nickel plated construction and needs only infrequent lubrication. The slats are made of a nylon composite, need no maintenance and can easily be replaced as single components without the use of special tools. Ryson has a full staff of factory trained service technicians ready to assist. All of our service techs are PMMI Certified Trainers. All of these factors contribute to Ryson’s low total cost of ownership.
The Ryson modular design makes it easy to field modify our vertical conveyors in case of unplanned installation changes or to reconfigure and repurpose the spirals at a later date. Click to see some examples:
All Ryson Spiral Conveyors are equipped with an automatic chain tensioning device and built-in overload protection as a standard. This helps save both the Vertical Conveyor and the product it is conveying.
Ryson Spirals are powder coated carbon steel with choice of any standard RAL color. They are also available in hybrid versions suitable for wet environments or stainless steel versions for washdown applications.
- Specs & Configurations
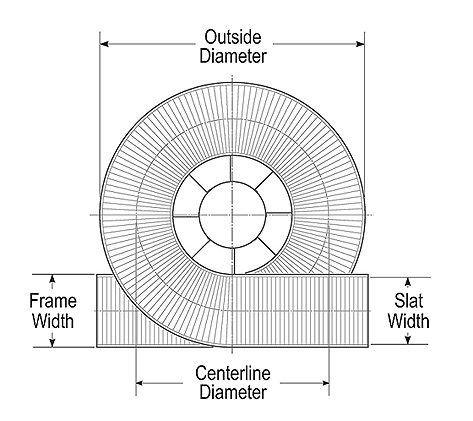
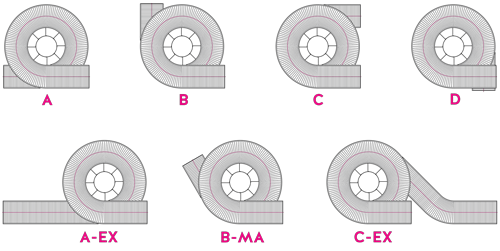
Most Common Vertical Conveyor Models
Diameter
Diameter
Width
Width
- Vertical Conveyor Videos

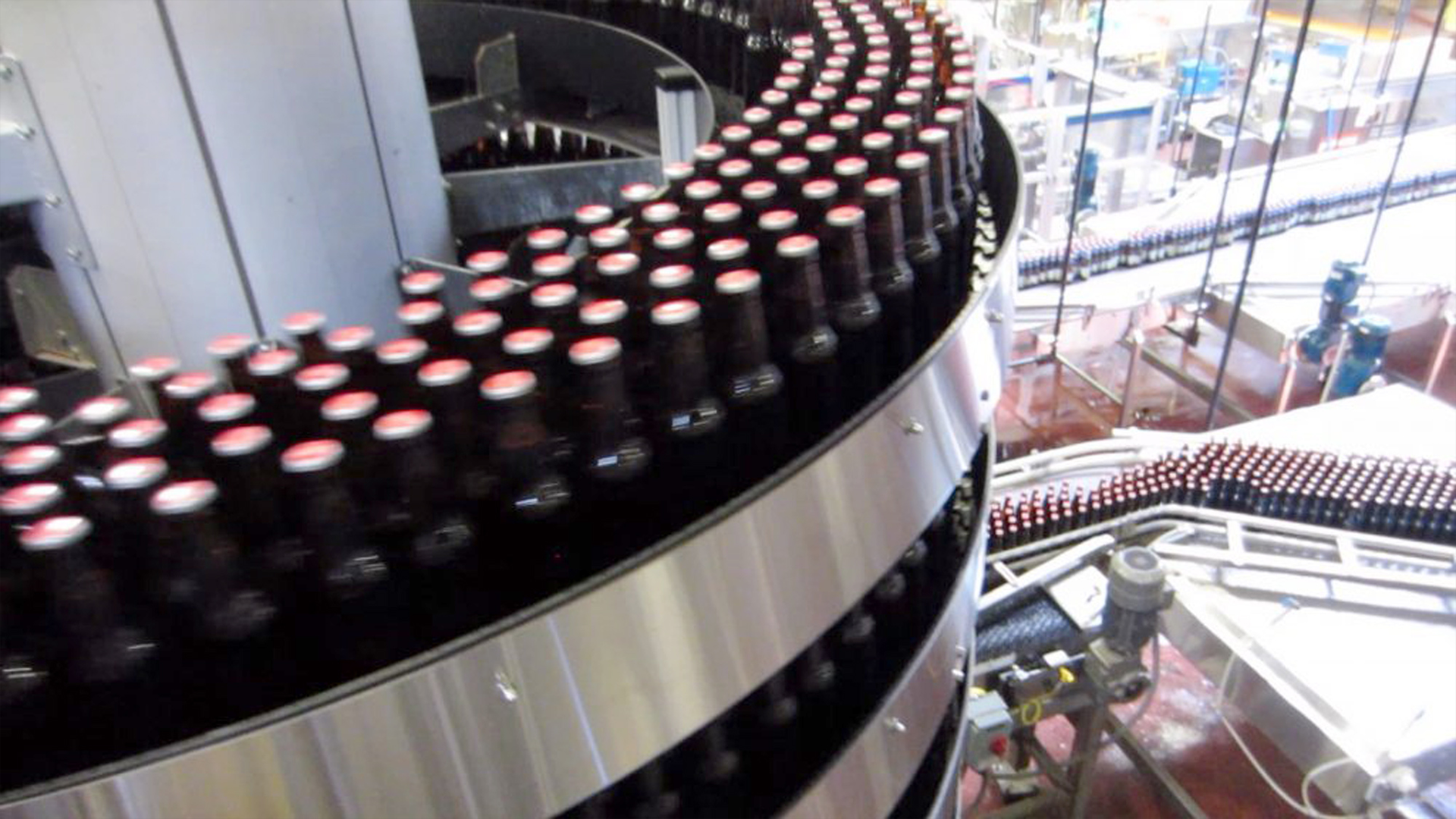
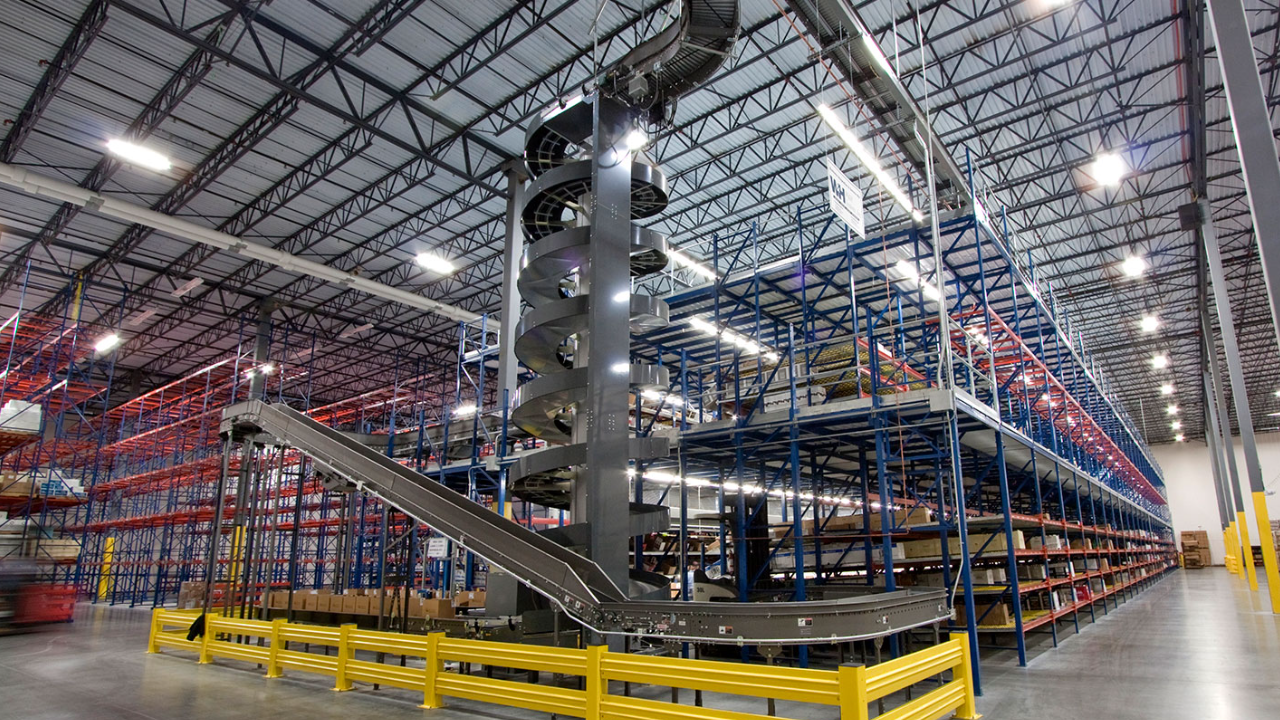
Related Articles
A quick comparison
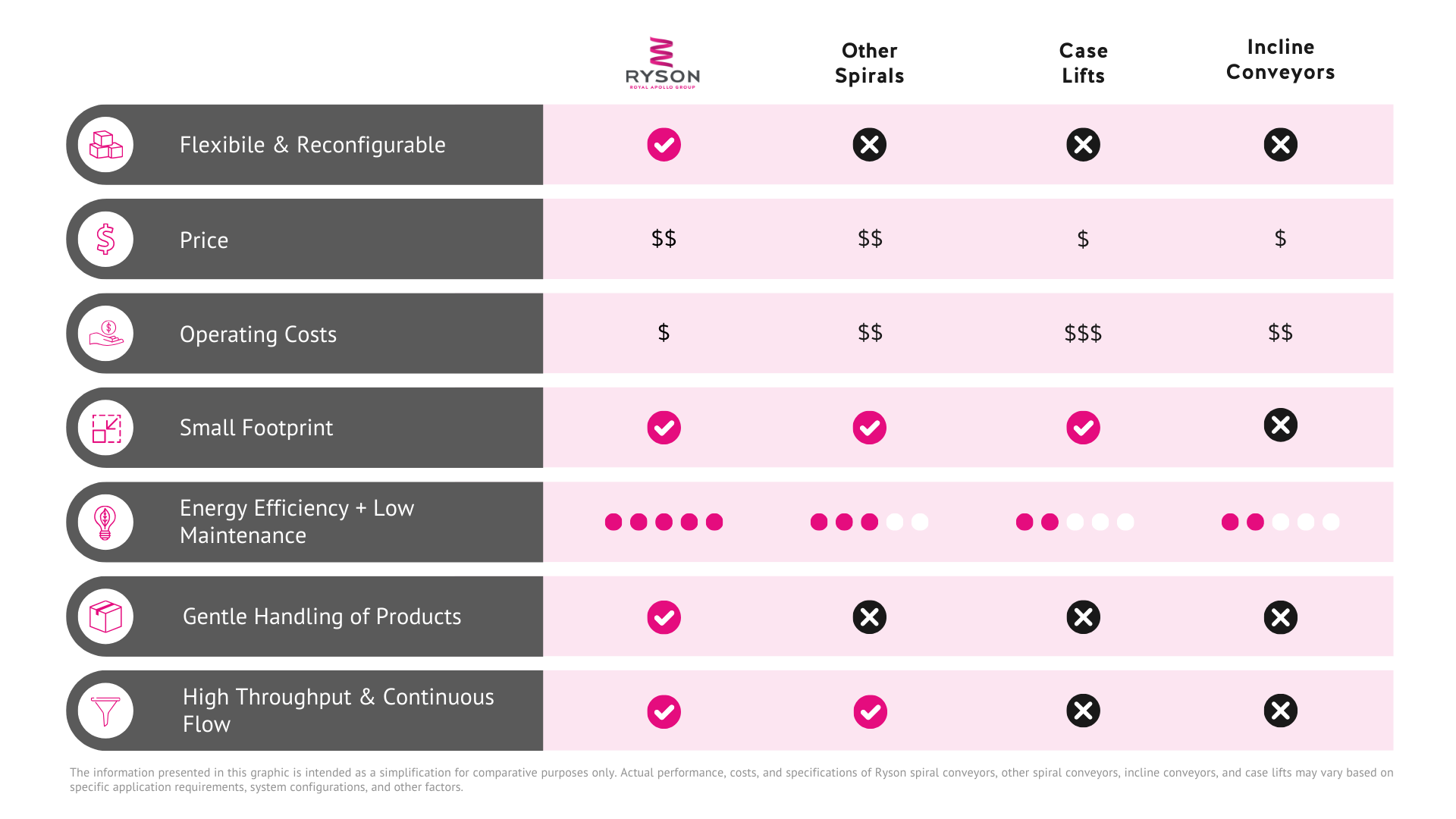
Ryson Spiral Conveyors lead the way with unmatched flexibility, compact design, and energy efficiency. This makes them the top choice for operations focusing on a high throughput and continuous flow.
Unlike lifts or incline conveyors, which can be limited by space, maintenance needs, or stop-and-go movement, Ryson Spirals handle products gently while maintaining low operating costs over time.
For facilities needing adaptable, efficient, and space-saving solutions, Ryson Spirals are a smart, long-term investment.
What is a spiral conveyor?
A spiral conveyor is a vertical material handling system that moves products upward or downward in a helical path around a central tower. This space-saving design allows for continuous vertical transport while maintaining a compact footprint.
What is the difference between a vertical reciprocating conveyor (VRC) and a spiral conveyor?
A VRC uses a platform to convey cases vertically, it functions like an elevator. Both offer vertical transportation. The main difference is how they handle different product sizes, their throughput capacity and mechanical operation.