New Space-Saving Model 1300-500 Spiral
We are happy to announce that we have a new model in our Spiral Catalog. The 1300-500 is a new model that has similar functionality to our 1600-500, but is built on a smaller frame.
The 1300-500 means that the footprint has gone from 7′-4.5″ to 6′-6″. It may not seem like a big change. But when you are fighting for every inch on your manufacturing floor, it can make a big difference.
This model 1300-500 was designed because we are finding that many companies are replacing older solutions with our Spiral Conveyors. Some of the units we are replacing have a smaller footprint. This small change allows us to offer a better solution that uses the exact same footprint. Therefore the need to reconfigure ancillary machinery is avoided. It’s just a simple pull and switch.
The Spirals pictured to the right are the first 1300-500’s that we have built. They also have some unique features that will aid in their application. They will be conveying 50 lb sacks of powder in a very dusty environment. So to help with cleaning, special perforated under cover plates, powder-coated load arms and stainless-steel side guiding was specified.
Our conveyors are quickly becoming recognized as a top solution for vertical conveying. They offer reliability, consistency and have an outstanding up-time record. Their low maintenance, long efficient up-time record – and the fact that they can be field modified to meet emerging line changes – gives them a very low cost of ownership over time.
You can find out more about our Spiral Conveyors on our very own YouTube Channel.
Ryson Sales Team Conference
This week the Ryson Sales Team all gathered at Ryson headquarters for a sales summit and team building.
This 3-day event gave the Ryson Sales Team the opportunity to discuss best practices, update each other on market trends and discuss matters that helps them be more effective team members. They also took the opportunity to meet with other Ryson departments, including marketing, engineering and service.
Clear communication ensures that everyone on the team understands the company’s objectives, product value propositions, and customer pain points. It also minimizes misunderstandings and redundant efforts, especially in high-stakes situations like responding to an urgent client request or preparing a customized proposal. Ultimately it clears the way for better customer service, something Ryson takes very seriously.
When sales teams communicate effectively internally, they can present a unified front to customers. A cohesive team ensures consistency in messaging, avoids contradicting statements, and builds trust with clients. This is particularly important when dealing with specialized equipment, as customers rely on accurate, clear, and comprehensive information to make purchasing decisions. Team-building activities encourage a culture of collaboration, allowing team members to brainstorm solutions together, and with their customers. With open communication, teams can leverage diverse perspectives and skills to innovate and address customer needs more effectively.
Included in this week’s agenda, representatives from PMMI, MHI and MHEDA will present benefits the offer to their members. All of these organization are outstanding and offer many resources to their members. This of course gives us the opportunity to learn how to make better leverage these benefits.
By investing in team building and fostering effective communication, the Ryson Sales Team becomes a more effective and efficient sales force and becomes more adaptable to the demands of a highly technical and competitive industry. Ultimately this will help improve our integrator relationships and help bolster our customer support and service. Get to know the Ryson Team Better.
New Year, Focus on 2025
HAPPY NEW YEAR~ As we put 2024 in our rear view mirror, we start to focus on 2025.
While our core business has been steady, we are finding growth in plant upgrades and retrofits. Whether companies are looking to retrofit older equipment, or investing in increased efficiency, the Ryson phone is ringing.
We are looking forward to focus on 2025 and working with our partners to develop solutions the fit their needs. We have found that these areas have great growth potential this year.
“2025 is the year to thrive as innovation, sustainability, and automation drive industry growth. Ryson is poised to capitalize, expanding our reach and redefining efficiency in the supply chain, packaging & manufacturing and material handling solutions” – Taoufik “TK” Haddadi, Ryson Sales Manager
Industrial Business
The global industrial sector in 2025 is expected to experience moderate growth, driven by advancements in automation, green technologies, and reshoring trends. Manufacturing is likely to continue its recovery post-pandemic, bolstered by increasing demand for machinery, energy-efficient systems, and smart factory solutions. Governments are expected to invest in infrastructure, green energy, and digitalization, boosting industries such as construction, heavy machinery, and logistics.
Challenges may arise from geopolitical tensions, rising raw material costs, and labor shortages, particularly in advanced economies. However, the push toward sustainability, especially in sectors like steel and cement, will provide new opportunities. The industrial automation sector is poised to grow, as companies seek to improve efficiency and reduce reliance on manual labor.
Warehousing and Logistics
The warehousing sector is poised for continued expansion in 2025, driven by growing demand for e-commerce and supply chain transformation. The shift toward near-shoring and onshoring of manufacturing will increase the need for more localized, efficient warehousing facilities. Automation, including the adoption of robotics, AI, and autonomous vehicles, will continue to reshape logistics, improving inventory management, order fulfillment, and delivery efficiency.
The ongoing trend towards “just-in-case” inventory systems—replacing the previous “just-in-time” models—will necessitate more extensive warehousing capacities, especially for critical goods. Demand for sustainable and energy-efficient warehouse solutions will also rise, as companies strive to meet environmental, social, and governance (ESG) goals.
Consumer Packaged Goods (CPGs)
The CPG sector in 2025 is expected to benefit from continued growth in demand for convenience products, especially as consumer lifestyles become more fast-paced and health-conscious. Innovation in sustainable packaging, plant-based foods, and functional beverages will drive consumer interest. Brands are increasingly focusing on sustainability, with consumers demanding more eco-friendly packaging and supply chain transparency.
However, inflationary pressures, supply chain volatility, and rising raw material costs may affect profit margins. The shift toward direct-to-consumer (DTC) models and personalized offerings is likely to continue, fueled by digital transformation and e-commerce integration. Companies that adapt to changing consumer preferences, such as offering healthier or more sustainable options, are likely to see the most growth.
Online Retail
Online retail will remain a dominant force in 2025, driven by consumer demand for convenience, personalization, and an enhanced shopping experience. E-commerce platforms will continue to innovate, leveraging AI and augmented reality (AR) to improve customer engagement and shopping experiences. Increased adoption of omnichannel strategies, where consumers move seamlessly between online and offline shopping, will be critical for success.
The subscription-based model is likely to grow further, with consumers increasingly preferring automated deliveries for everyday items. Supply chain efficiency will be critical, with companies investing heavily in warehousing automation and AI-driven logistics. However, the sector will face regulatory challenges, particularly around data privacy, taxation, and sustainability.
As we focus on 2025, the economic outlook shows positive growth prospects for industrial businesses, warehousing, CPGs, and online retail, though companies will need to navigate challenges such as inflation, labor shortages, and regulatory pressures. Sustainability and technology adoption will be key drivers of success across these sectors. To find out more about Ryson’s Vertical Conveying Solutions, follow us on YouTube!
Wishing You Happy Holidays And An Amazing 2025!
Happy Holidays from all of us at Ryson!
As the holiday season sweeps in, we at Ryson are reflecting on a year filled with milestones, teamwork, and incredible partnerships.
This time of year isn’t just about winding down—it’s about appreciating the journey we’ve shared with all of you.
Two weeks ago, we had the privilege of hosting our Christmas Lunch with our CEO, Claudia van den Pol from Royal APOLLO Group, who joined us from Holland to celebrate the season and Ryson’s accomplishments. On that day everyone received a Christmas gift and our team also wore our brand new polo shirts for the first time for a nice group shot!
We were also happy to celebrate with Claudia at our corporate Christmas Party, shortly after. The party brought the team together to toast to a year of hard work and exciting progress.
We’re immensely grateful to our partners, customers, and team for making 2024 a success.
Your trust, collaboration, and dedication are at the heart of everything we do.
From our Ryson family to yours, Happy Holidays and a Happy New Year! Here’s to an even brighter and more successful 2025.
Celebrating the Retirement of a Dedicated Employee
This month, we celebrate the well-earned retirement of Mary Stanek, our Accounting Assistant, who has been an integral part of the Ryson team since December 2008.
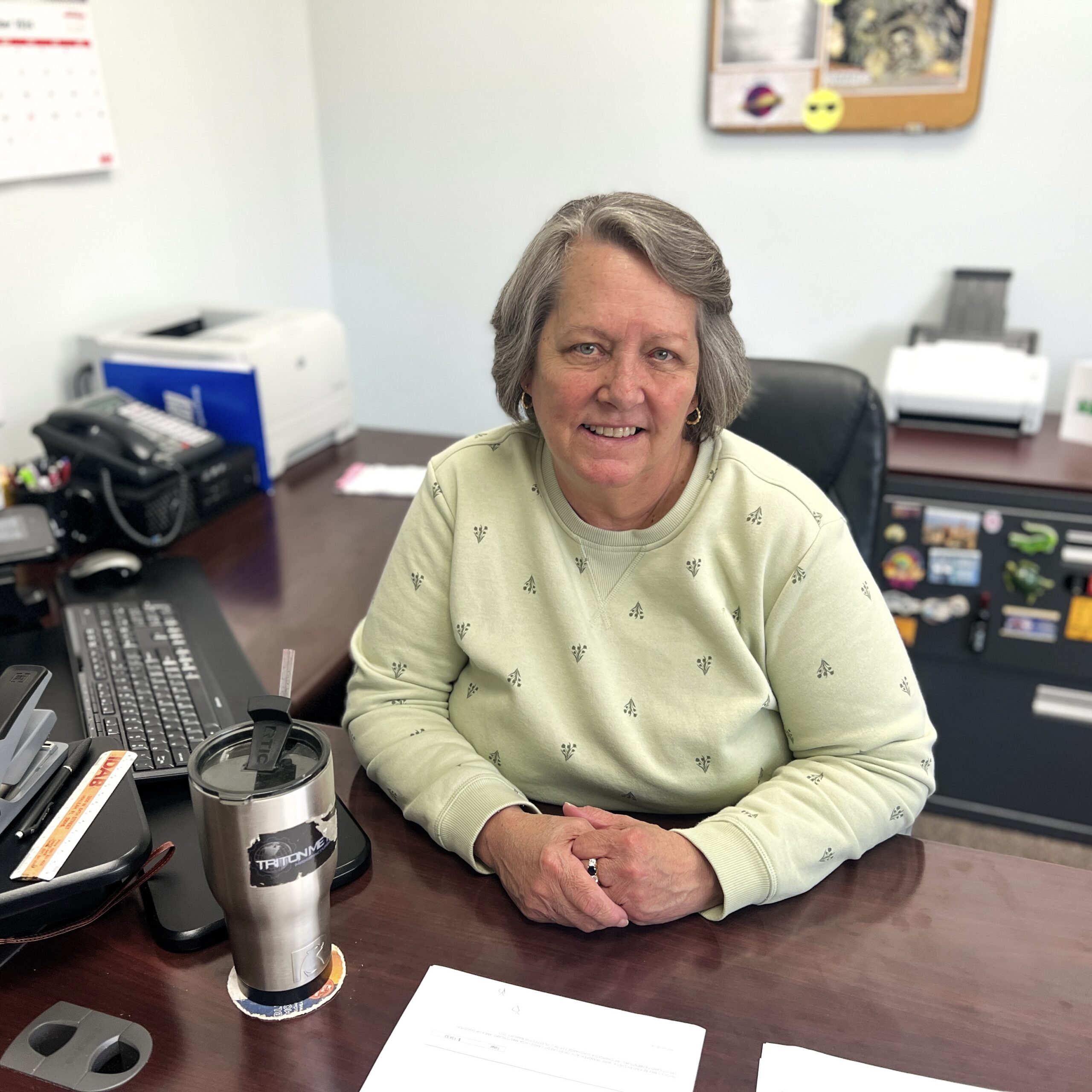
Over the past 16 years, Mary has not only kept our accounting in top shape but has also been the go-to person for ensuring the team in the shop always had the tools and equipment needed to build our spirals. Behind the scenes, her contributions kept Ryson moving forward. Mary also loves plants and gardening and became the “Plant Mom” around the office.
Reflecting on her time here, Mary shared a story from her very first week that left a lasting impression:
“It was my first week, and it happened to be pizza party week. I remember the owners were handing out Christmas bonuses during that pizza lunch. Since I had just started, I didn’t expect anything, but to my surprise, they handed me a bonus check. I hadn’t even earned anything with them yet. So I thought to myself, ‘This must be a good company.’ And I was right.”
When asked for advice to share with the team as she wraps up her career, Mary said:
“Be grateful that you’re working at a good place. That is something special.”
And what will Mary miss the most about working here?
“The people—my colleagues and the vendors I’ve worked with over the years. The relationships I’ve built here mean a lot to me.”
Mary’s dedication, kindness, and unwavering support have made a lasting impact on all of us. She’s been the quiet strength behind so many of Ryson’s successes, and her presence will be deeply missed. We celebrated Mary’s retirement at our monthly staff luncheon.
Mary, thank you for everything. We wish you a retirement filled with joy, relaxation, and a lot of time to work on your gardening projects. You deserve it all!
Boosting Packaging Line Efficiency with Spiral Conveyors
What’s Holding Back Your Packaging Line Efficiency?
Every packaging operation has its challenges—whether it’s limited floor space, product variety, or the need for faster throughput. For many manufacturers, these hurdles can make it tough to keep up with demand while staying efficient. That’s where spiral conveyors come in. By optimizing space and enhancing flexibility, they’re helping businesses reimagine their packaging lines for better efficiency and flow.
Let’s dive into how Spiral Conveyors could be the solution your operation needs.
Why Packaging Line Efficiency Matters
Efficient packaging lines are essential for meeting production targets, reducing costs, and maintaining product quality. Yet, the challenge lies in maximizing output while using minimal resources, particularly in space-constrained environments. This is where spiral conveyors shine.
Space Optimization with Spiral Conveyors
Traditional conveyor systems often require sprawling layouts, consuming valuable floor space. Spiral conveyors, however, transport goods vertically, utilizing overhead space. This compact design is ideal for facilities aiming to add new lines or replace outdated equipment without requiring large-scale renovations.
By reducing the operational footprint, spiral conveyors free up floor space for other critical activities, ensuring smoother material flow and minimizing bottlenecks.
Enhanced Line Flexibility
One standout feature of spiral conveyors is their adaptability. They can handle diverse packaging types—whether bottles, cans, (Mass Flow Spirals) or cartons (Unit Load or High Capacity Spirals) —without needing extensive modifications. Equipped with customizable attachments, these conveyors ensure proper alignment and orientation of products throughout the process. This flexibility supports the introduction of new products or packaging formats with minimal downtime.
Easy Integration and Scalability
As production demands fluctuate, the ability to reconfigure or expand a packaging line becomes critical. Spiral conveyors, with their modular design, offer seamless integration into existing systems. This scalability allows companies to quickly adjust layouts, boosting efficiency and responsiveness to market demands.
Reducing Maintenance Hassles
Downtime is every manufacturer’s nightmare. Spiral conveyors are designed for easy maintenance, with accessible components that streamline troubleshooting and repairs. Features like vertical accumulation zones further enhance efficiency by maintaining product flow during temporary stoppages, reducing costly delays.
Final Thoughts
For businesses aiming to improve packaging line efficiency, spiral conveyors present an innovative solution. By optimizing space, enhancing flexibility, and simplifying scalability, these systems help companies stay competitive in demanding markets. Whether you’re planning an upgrade or designing a new line, spiral conveyors can play a pivotal role in achieving operational excellence.
If you’re looking to optimize your packaging line, consider how spiral conveyors could fit into your strategy—and watch your efficiency soar. Check out some Ryson Videos on our YouTube Channel.
Ryson Shipping – A Cornerstone of our Pledge to Customer Service
Ryson Shipping: The Unsung Heroes Behind Great Customer Service
In the world of industrial manufacturing, every role matters. Among our key staff, the shipping team stands out. They ensure our Spiral Conveyors reach their destinations on time, every time. This work is essential. Not only for logistics but also for maintaining strong customer relationships—something Ryson takes very seriously.
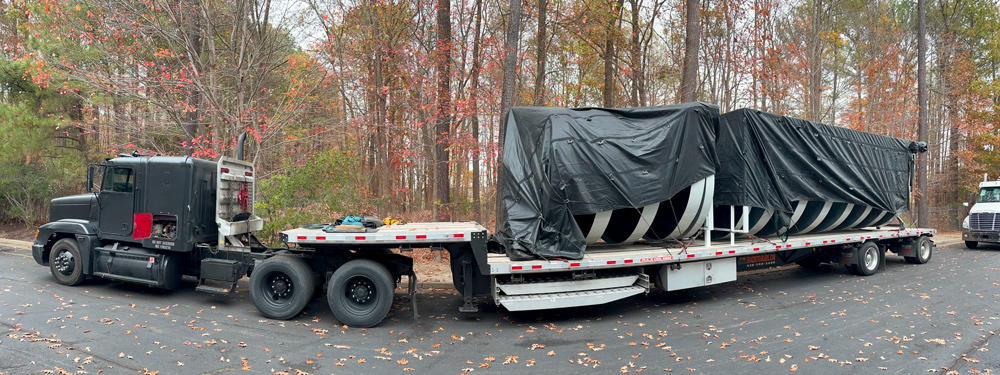
The Role of a Shipping Coordinator
A shipping coordinator’s responsibilities extend far beyond overseeing deliveries. They are the architects of the delivery process, coordinating with production teams, assisting in warehouse operations, and navigating transportation challenges to ensure seamless deliveries. From selecting reliable carriers to handling last-minute changes, their role demands a balance of strategic planning, real-time problem-solving, and meticulous attention to detail.
In our industry, this role is even more critical. Delays in delivering Spiral Conveyors can ripple across the supply chain, causing disruptions for customers who rely on timely shipments to complete plant-wide implementations. The shipping team ensures that these expectations are met, fostering trust and reliability—key tenets of strong business relationships.
Recognizing Their Contributions
It’s easy to overlook the contributions of shipping coordinators. They can go unnoticed if everything is delivered on time. That is why we would like to thank our Shipping Coordinator – Nathan Cary. His hard work and dedication helps uphold the Ryson standard – Both with our quality product and our professional service.
On-Time Deliveries: The Backbone of Customer Service
A company’s reputation is built on its ability to deliver quality products on schedule. While product innovation and manufacturing precision are critical, they lose their impact if the product doesn’t arrive when promised. This is where our shipping coordinator shines. Timely deliveries of our Spiral Conveyors not only meet contractual obligations but can at times exceed customer expectations. When a shipment arrives exactly as planned, it sends a powerful message: your business values its customers’ time and operational needs.
Consider the scenario of a manufacturing plant awaiting a spiral conveyor to complete its production line or pick module in a warehouse. A late delivery of our equipment could result in costly downtime, impacting not just the customer but the entire supply chain. This is particularly true in warehousing, where often times our Spirals are built with mezzanines before any other conveyors are installed. View videos about our Spiral Conveyors.
Holiday Logistics Solutions – Get your Distribution Center Ready
Is your distribution center or warehouse ready for the holiday rush? Holiday Logistics Solutions
The holiday season is upon us, and with it comes the shopping frenzy of Black Friday, Cyber Monday, and the weeks leading up to the festivities. For retailers and e-commerce businesses, this time of year brings skyrocketing demands that can stretch logistics operations to their limits. To meet these challenges head-on, efficiency and reliability are key—and that’s where Ryson Spiral Conveyors come in.
The Holiday Challenge: Managing Unprecedented Demand
Black Friday and the holiday season mean a surge in orders that can overwhelm even the most well-prepared distribution centers and warehouses. Bottlenecks, delays, and customer dissatisfaction are common risks, especially when traditional logistics systems struggle to handle the pressure.
Ryson Spiral Conveyors offer a reliable, high-performance solution to keep your supply chain running smoothly during this critical time—and all year round.
Holiday Logistics Solutions – How Ryson Spirals Make a Difference
1. Reliability That Minimizes Downtime
During the holidays, every second counts. Ryson Spirals are engineered for continuous operation, ensuring smooth and uninterrupted vertical movement of goods. Their durable design reduces the risk of downtime, helping retailers keep up with demand without delays or disruptions.
2. High-Speed, High-Throughput Performance
Speed is non-negotiable when meeting tight holiday deadlines. Ryson Spirals are designed for high-speed and high-throughput operations, efficiently handling large volumes of parcels, boxes, and even fragile goods. Their compact vertical design allows for seamless integration into fast-paced fulfillment systems, enabling quicker order processing.
3. Space Optimization for Busy Warehouses
Space is always at a premium in warehouses, especially during the holidays when order volumes spike. Unlike traditional conveyors that take up valuable floor space, Ryson Spirals utilize vertical space efficiently. This space-saving design allows distribution centers to maximize operational capacity without requiring additional square footage.
4. Maximizing Throughput During Peak Periods
From Black Friday to Cyber Monday and beyond, Ryson Spirals keep goods moving. Their continuous flow design eliminates bottlenecks, ensuring orders are processed swiftly and accurately. This high throughput is crucial for maintaining customer satisfaction during the busiest shopping season of the year.
Perfect for B2C Retailers and E-commerce Operations
Ryson Spiral Conveyors are an ideal fit for the fast-paced world of e-commerce and retail. Whether in multi-level fulfillment centers or last-mile delivery hubs, they support efficient routing, packing, and movement between storage, picking, and shipping zones.
Their flexibility ensures they can adapt to the unique needs of any operation, from handling different package sizes to integrating with existing conveyor systems.
Your Partner in Holiday Success
The holiday season is a make-or-break time for many businesses, and having the right logistics solutions in place is essential. Ryson Spiral Conveyors provide the reliability, speed, and efficiency you need to tackle holiday challenges while exceeding customer expectations.
Prepare your distribution center with Ryson Spirals and deliver joy to your customers—one package at a time. Watch this video for more information and interesting footage!
Ryson Celebrating Thanksgiving
At the Ryson headquarters we also celebrated an early thanksgiving with a delicious potluck.
The entire Ryson team would like to wish you a beautiful thanksgiving weekend with your loved ones and amazing food!
Why Ryson Spirals Are the Best Choice for Retrofit Projects
Spirals for Retrofit Projects – How suited are they?
As industries grow and adapt, many businesses are opting to modernize their existing facilities instead of starting from scratch. Retrofitting, or upgrading brownfield facilities, requires innovative solutions that work seamlessly with the current setup. This is where Ryson Spiral Conveyors stand out as the ideal choice.