In the next few weeks these impressive Mass Flow Spirals will ship and be installed at a major bottling plant. They will be instrumental in freeing up some much needed production space.
Once installed, these Spirals will help open up operational traffic flow. The existing layout had several floor-mounted conveyors that prevented transportation of raw materials from a storage area through the production facility. By sending finished product “up and over”, valuable floor space will be better utilized. It would also enhance the flow of materials through the plant.
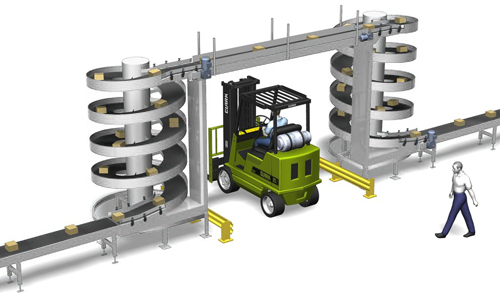
This concept can be used with both our standard Spirals and our Mass Flow Spirals.
The integrator on this project is Sentry ProMach. They specified our Model 1900-400 Spirals – with a 16” wide conveying surface – to handle their customer’s line capacity of 2,000 cans per minute. They also have a 9 foot elevation change, that will allow forklifts to freely move through the previously contested area.
The Ryson Mass Flow Spiral Conveyor features special nesting slats that provide a smooth and reliable conveying surface. This consequently allows a gentle side transfer on and off the spiral with no gap between it and the feeding conveyor.
Round units like cans, bottles and jars slide reliably on to, and off of the spiral in a smooth mass flow. They are commonly used to transport bottles to a filler, or send cans to a pasteurization area.
The Modular Advantage.
Ryson Spirals are customizable and modular. Therefore it is increasingly common that they replace older equipment in facilities. Our Spirals can be installed in the tightest of spaces – even if they have to be assembled in sections. Finally, Ryson Mass Flow spiral are space savers. They are available in powder coated steel, or stainless steel suitable for wet applications.
For additional information, visit our Mass Flow page, read other application stories, or watch our Video Brochure.