Ryson welcomes customer site visits with open arms.
Recently we hosted a customer visit to our manufacturing plant to inspect a Spiral prior to us shipping it. We set up the visit through a valued integrator partner PeakLogix, who traveled with their end-user customer.
This was a mutually beneficial site visit, because the spiral was specified to ship in two pieces to aid installation in a tight area upon delivery. It gave us the opportunity to show the customer the process of reassembly on-site. Additionally it gave them an idea of what to expect when it is delivered. In addition to product testing, our Service team also oriented the end customer on installation and preventative maintenance best practices.
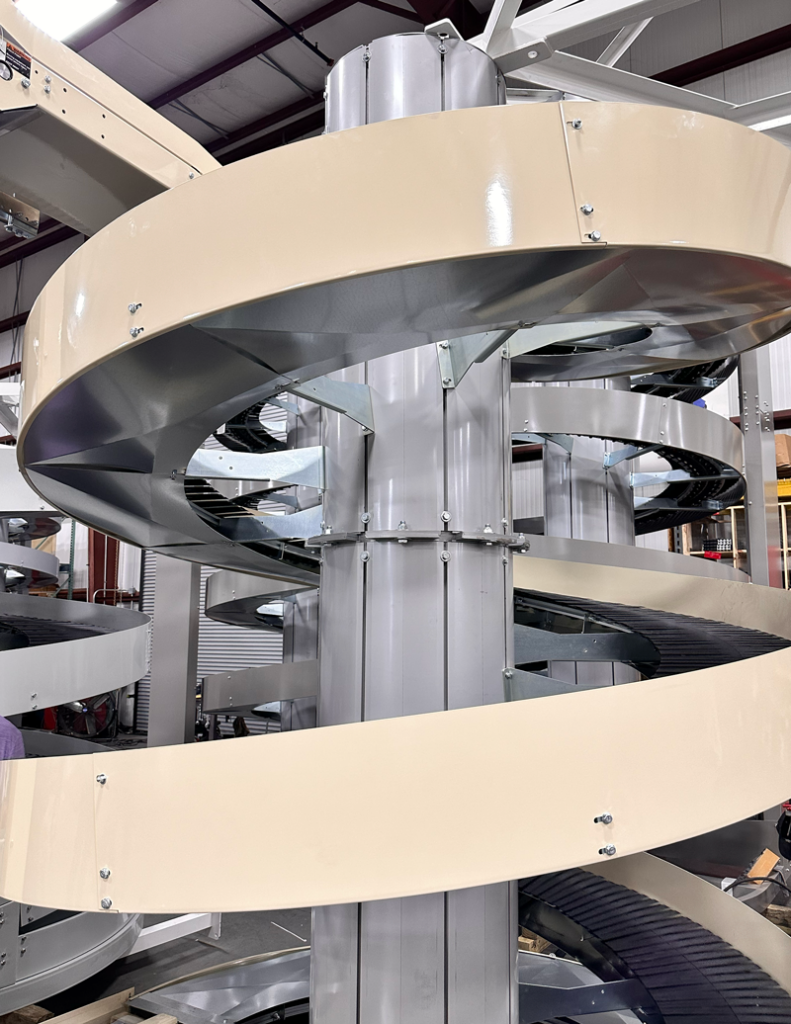
Our Spirals generally ship in one piece ready to run upon installation. However some of our larger models require partial disassembly to fit on a truck. In other instances, such as this one, our modular design allows the spiral to be constructed in multiple pieces to aid in installation in tight areas. A classic example is installation through a penetration in a floor between levels.
Ryson Modular Design
The Ryson modularity also comes in handy when a spiral is specified to replace older equipment. Often times customers wish to remove larger diameter belt curves, or slower VRC’s for the compact, and higher throughput Spiral Conveyor. Often times the installation area is surrounded by machinery and there may be a tight egress. This is where the modularity of our equipment really comes in handy.
The Ryson design team is always willing to work with the customer to come up with the most practical solutions. Find out more about our different Spiral Applications, or read some current installation stories from our weekly blog.