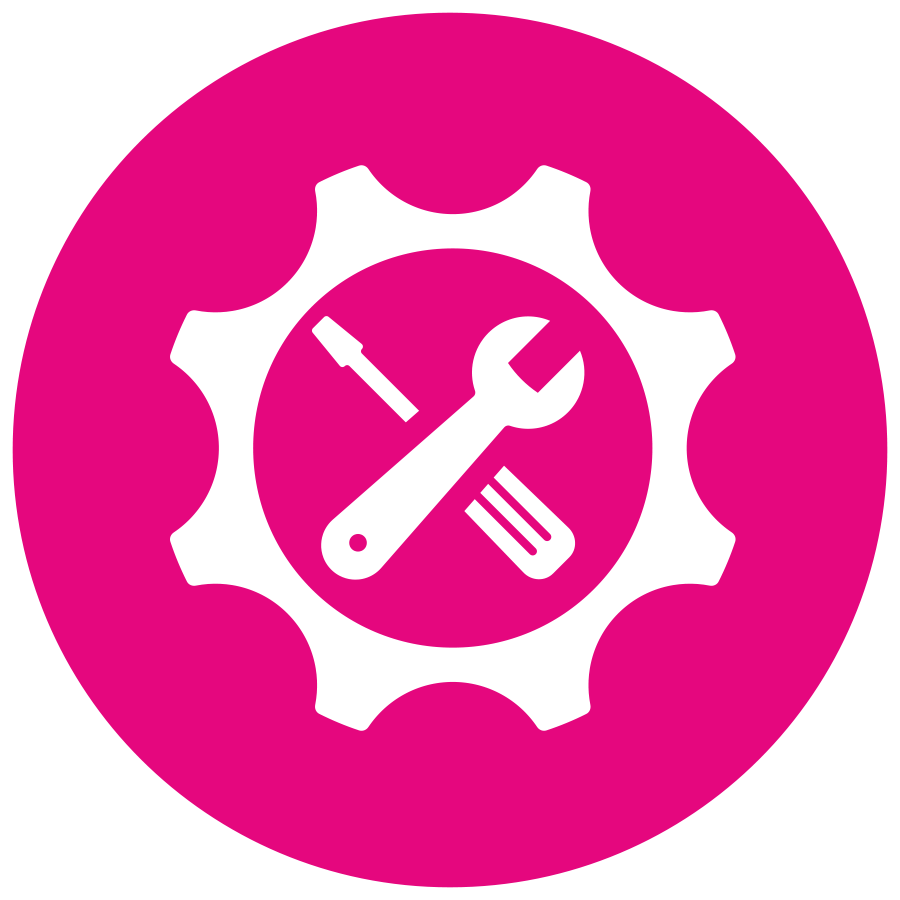
Proactive preventative maintenance in industrial settings can result in substantial cost savings. It can minimize unplanned downtime, reduce emergency repair expenses, extend equipment lifespan, and help improve operational efficiency.
Unplanned downtime is one of the most expensive risks manufacturers face. Often with costs ranging from $5,000 to $22,000 per minute depending on the industry and complexity of the operations. For a mid-sized facility, this can translate into over a million dollars in losses per year due to unexpected breakdowns. In fact, studies show that up to 42% of such downtime is caused by preventable equipment failures.
In contrast, preventative maintenance (PM) is relatively low in cost and highly predictable. It typically requires 1 to 4 hours of scheduled work during off-hours or production lulls. It can also often be completed with minimal disruption. Emergency repairs, on the other hand, can take anywhere from 8 to 24 hours or more — especially when diagnostics, part sourcing, and extensive labor are involved. For example, a conveyor motor that undergoes routine lubrication and inspection every quarter might require only a few hundred dollars per visit, but this investment could prevent a failure that would otherwise cost upwards of $120,000 in downtime and repairs. The return on investment in such scenarios can easily exceed 60 to 1.
Manufacturers who implement structured preventative maintenance programs often experience a 25–30% reduction in overall maintenance costs. A 35–45% reduction in downtime, and a 10–20% increase in equipment lifespan. The financial implications are clear: preventing even a single critical equipment failure each year can justify the cost of an entire preventative maintenance program. Beyond savings, this proactive approach enhances workplace safety, maintains consistent production levels, and reduces reliance on reactive, high-cost fixes.
Summary: Why Preventative Maintenance Pays Off
Factor |
Without PM |
With PM |
---|---|---|
Downtime Cost |
High, unpredictable |
Low, scheduled |
Lifespan |
Shortened |
Extended |
Repair Costs |
Emergency (higher rates) |
Standard (lower cost) |
Safety Risk |
Higher |
Lower |
Efficiency |
Disrupted |
Stable |
An increasingly popular solution for companies looking to streamline maintenance without building a full in-house team is the use of third-party maintenance contracts. These agreements typically provide scheduled inspections, parts replacement, and emergency response coverage. They are often at a fraction of the cost of internal maintenance operations. Leveraging third-party expertise ensures that preventative routines are consistently performed by specialists, reducing the likelihood of oversight while freeing internal staff to focus on core production tasks. This approach combines predictable maintenance costs with high-quality service and can be especially valuable for businesses with limited technical staff or specialized equipment needs.